通过静电组装法制备的 Al2O3 基纳米碳复合材料的受控微观结构和机械性能
摘要
这项工作报告了使用碳纳米颗粒 (CNP)-氧化铝 (Al2O3) 复合颗粒在微观结构控制下形成相互连接的碳层状 Al2O3 陶瓷。本研究中使用的 Al2O3 微粒是通过将平均直径为 150 nm 的纳米级 Al2O3 纳米颗粒造粒而获得的。然后,使用颗粒状的 Al2O3 和 CNP,使用静电组装方法制造 CNP-Al2O3 复合材料。使用固定量的 CNP,研究了 CNP 在粒状 Al2O3 表面上的装饰作为初级粒径和覆盖百分比的函数。值得注意的是,在 Al2O3 界面处获得了类似于晶界的碳颗粒互连层。还研究了不同粒径和CNP覆盖在Al2O3颗粒上的样品的力学性能,为通过复合陶瓷材料的微观结构设计控制力学性能提供了可能性。
介绍
众所周知,氧化铝(Al2O3)具有硬度高、耐磨性好、化学稳定性好等优良特性。另一方面,氧化铝的缺点是其断裂韧性差、高温强度低以及抗热震性差[1]。这促进了对微米和纳米尺度氧化铝基纳米复合材料开发的深入研究。据报道,在陶瓷基体中具有良好分散的纳米尺寸颗粒的功能性陶瓷复合材料不仅可以提高机械性能,如失效强度、断裂韧性、疲劳和耐磨性,还可以提高电、磁、热和光学性能 [2]。 ,3,4,5,6,7]。为了改善和控制陶瓷的机械性能,已经使用并报告了微结构孔隙率 [8, 9]、添加填料 [10] 和热处理曲线 [11, 12]。这表明通过控制 Al2O3 的微观结构,可以获得所需的 Al2O3 陶瓷力学性能。然而,大多数报道的工作仅采用在烧结前混合 Al2O3 粉末的简单方法,不足以对 Al2O3 陶瓷的微观结构和设计进行良好控制,导致其机械性能的可控性较差。在通过常规混合方法形成纳米复合材料时,由于添加剂颗粒的团聚,将纳米尺寸的添加剂颗粒均匀地装饰在指定的初级颗粒上仍然是一个巨大的挑战。由团聚引起的不均匀分布然后会对微结构设计以及陶瓷复合材料的性能产生不利影响。因此,本研究使用了一种通过静电吸附法自下而上组装的新方法,以证明获得良好的微观结构控制和设计的可行性,从而允许将受控的所需特性引入 Al2O3 陶瓷,例如光学、电学、和机械性能。作为Al2O3陶瓷复合材料的一种可能的添加剂,已经开发出各种形状的纳米碳材料,如纤维(碳纳米管(CNT)、纳米纤维)和板状(石墨烯)以及颗粒。这使得最近报道的碳基材料作为材料制造添加剂的应用成为可能。
在碳基氧化铝复合材料的开发中,Kumari 等人。据报道,通过改变碳纳米管添加的重量百分比和烧结温度,与纯氧化铝相比,碳纳米管 (CNT)-氧化铝复合材料的热导率提高了 60% 至 318% [4]。除此之外,由于碳基复合材料在发电、运输和制造等应用中具有卓越的摩擦学特性,许多研究人员将他们的兴趣集中在碳基复合材料的开发上 [13, 14]。据报道,具有碳增强表面的陶瓷表现出改善的耐磨性和降低的摩擦系数。尽管关于在氧化铝和氧化锆上使用碳纳米纤维 (CNF) 增强机械强度的报道存在争议,但大多数作者都报道了机械性能的改善。最近一项关于碳纳米管对氧化铝蠕变性能的研究得出了相反的结论,因为据报道,根据碳纳米管的添加量,蠕变强度可能由于晶界滑动的障碍或晶界的促进而增强或减弱。扩散或滑动,分别[15]。与此同时,Crepo 等人。据报道,氧化石墨烯增强氧化铝复合材料比 CNF 增强氧化铝具有更好的抗蠕变性 [16]。此外,由于石墨具有优异的润滑性能,碳基材料是固体润滑剂应用的良好候选者。据报道,在干摩擦过程中,碳基复合材料会因碳的脱落及其与受影响接触区域上的陶瓷碎屑的结合而产生润滑膜 [13]。然而,大多数报道的工作涉及通过悬浮液的超声混合或传统的机械研磨来使用单一混合,并且没有证明在陶瓷上控制碳材料的装饰导致形成微结构控制的碳-基于陶瓷。因此,在本研究中,CNP-Al2O3 复合材料是使用静电吸附组件制造的,这在其复合组件的组装和设计中提供了更多的可控性。在这项工作中使用的 Al2O3 微粒是使用纳米尺寸的 Al2O3 颗粒的控制造粒获得的。然后,将获得的粒状 Al2O3 微粒用于形成碳 CNP-Al2O3 复合材料。该研究是通过将碳纳米球的量从 0.3、0.6 和 1.0 vol%(体积百分比)和所用氧化铝颗粒的平均尺寸变化来系统地进行的。然后使用三点弯曲和压痕测试表征碳基复合材料样品的机械性能并与整体氧化铝样品进行比较。还讨论和阐明了所获得的显微组织与力学性能之间的相互关系。
方法
平均直径为 150 nm 的氧化铝纳米粒子购自 Taimei Kagaku Kogyo Co. 并作为前驱体获得颗粒状的 Al2O3 微粒。使用 Al2O3 微粒与丙烯酸粘合剂的混合物的喷雾干燥进行造粒。然后将 Al2O3 微粒过筛以获得三种不同的平均直径 37、62 和 98 μm,然后将其用作初级粒子。平均直径为 260 nm 的 CNP 购自 Tokai Carbon Co.,用作添加剂纳米颗粒。由于CNP是疏水性的,不能分散在水介质中,因此先将其分散在SDC(脱氧胆酸钠)溶液中,然后进行亲水化处理以进行后续涂层。将 40 毫升 0.1 wt% SDC 溶液加入到 1 g CNP 中,并通过超声处理分散 30 分钟。然后,将溶液离心并使用离子交换水洗涤3次,该离子交换水通过用混合器搅拌水来进行。之后,使用聚阳离子和聚阴离子进行表面电荷的改性。聚二烯丙基二甲基氯化铵 (PDDA)(平均分子量 100,000 至 200,000,Sigma-Aldrich)和聚苯乙烯磺酸钠(PSS)作为聚阴离子(平均分子量 70,000,Sigma-Aldrich)分别用作聚阳离子和聚阴离子。之后,将 SDC 包覆的 CNP 交替浸入 PDDA、PSS 和 PDDA 中,以诱导稳定的表面正电荷。在吸附过程之后,剩余的悬浮液被干燥然后收集。在第一次调查中,使用直径为 62 μm 的 Al2O3 颗粒,并进行了 CNP 对 Al2O3 颗粒覆盖率控制的可行性。添加的 CNP 的体积百分比为 0.3、0.6 和 1.0 vol%。在研究 Al2O3 尺寸的影响时,固定的 CNP 添加量为 0.6 vol%,而平均直径为 37、62 和 98 μm 的 Al2O3 颗粒用于复合材料的形成。首先使用直径为 12 mm 的模具对 CNP-Al2O3 复合颗粒进行单轴压制。施加的压力为300 MPa,保持时间为5 min。之后,将得到的颗粒插入到装有 h-BN 粉末的石墨模具中进行热压烧结(Diavac Inc. Ltd.)。在真空气氛(8 × 10 -3 Pa) 在 1350 °C(加热速率为 10 °C/min)下保持 2 h,压力为 30 MPa。使用 S-4800 场发射扫描电子显微镜(FE-SEM,Hitachi S-4800)观察 CNP-Al2O3 复合材料的形貌和获得的烧结微观结构。 zeta 电位使用 Otsuka Electronics Co. Ltd.、ELSZ-1 和 Micro Tech Nission、ZEECOM Co. Ltd. 测量。至于机械性能测定,使用 3 点弯曲试验测量所得样品的弹性模量.首先将样品切成条状试片,并使用平面磨床微调尺寸。制备的试样尺寸为3 × 4 × 40 mm。之后,分别使用0.5-mm氧化铝和30和9 μm等级的金刚石膏进行抛光。三点弯曲试验是使用 Instron 型紧凑型试验机测量的。首先,应力(σ ) 使用等式计算。 1 其中,l , b , 和 h 是每个试件的跨距和尺寸,而P 表示负载。接下来,绘制应力和应变之间的关系,并根据最小二乘法的斜率计算弹性模量。横梁速度为0.02 mm/min,跨度为30 mm。
$$ \sigma =\frac{3 lP}{2 bh} $$ (1)使用压痕进一步评估复合样品的硬度特性。所使用的洛氏压头由菱形 (E i =1050 GPa, υ =0.20) 具有标称曲率半径 R =200 嵌入顶角为 120° 的锥形尖端。将压头设置在 Instron 型测试仪(Sanwa Instruments)中,并以 0.05 mm/s 的十字头速度压入固定深度(20 μm)。压痕过程中获得的载荷用称重传感器(TCLZ-100KA,东京Gakko)测量,压痕深度用非接触式静电位移计(VE-222,小野测器)测量。
结果与讨论
图 1 显示了交替涂覆 PDDS 和 PSS 后,Al2O3 颗粒和 CNP 的表面电荷 zeta 电位。可以观察到氧化铝和CNP在三层涂层后分别表现出+ 55和- 55 mV的zeta电位。在 CNP 和 Al2O3 微粒上进行三层涂层后获得的 zeta 电位是稳定的。图 2 的 SEM 图像显示了 CNP 添加量为 0.3、0.6 和 1.0 vol% 的 CNP-Al2O3 复合材料的表面形貌。吸附在 Al2O3 颗粒表面上的 CNP 体积百分比增加。重要的是要注意 CNP 均匀分布在整个 Al2O3 表面,没有团聚迹象,这体现了 EA 方法获得均匀分布的优势。观察到的 CNP 的粒径约为 260 nm。通过将 CNP 的添加量固定在 0.6 vol% 并将 Al2O3 微粒的尺寸从 37、62 和 98 μm 改变,CNP 在 Al2O3 颗粒表面的分布如图 3 中的 SEM 图像所示。从SEM图像的观察可以看出,随着粒径的增加,吸附在表面的CNP的量也相应增加。由于与较小的 Al2O3 颗粒相比,较大的 Al2O3 颗粒具有较低的总表面积,因此与较小的 Al2O3 颗粒相比,可用于吸附 CNP 的集体表面积也较低。因此,在 CNP 添加量为 0.6 vol% 的情况下,较大量的 Al2O3 颗粒的整体表面积较小,因此会吸附更多的 CNP。结果,观察到吸附在 Al2O3 表面上的 CNP 量随着 Al2O3 颗粒的直径尺寸增加而增加,这导致 CNP 吸附在 98 μm Al2O3 颗粒表面上的密度更高。另一方面,随着粒径的减小,CNP 吸附在 Al2O3 上的可用总表面积增加,因此,由于悬浮液中的 CNP 量不足(固定的 0.6 vol%),观察到 CNP 的稀疏分布)。使用CNP-Al2O3复合材料在界面处高倍放大得到的烧结显微组织如图4所示。从图4a中的SEM图像可以看出,获得的显微组织反映了获得的CNP-Al2O3复合材料的形状.值得注意的是,晶界沿晶界相连形成网络。通过观察沿晶界形成的 CNP 网络,可以确定 CNP 分布在 Al2O3 颗粒表面的均匀性。该结果表明通过设计复合前驱体获得微结构可控的复合材料是可行的。从图 4b 中更高放大倍数的 SEM 图像中,可以观察到在 Al2O3 晶界界面之间存在碳层。这表明在热压烧结过程中,CNP 在 Al2O3 颗粒之间的烧结导致沿晶界形成均匀的碳层涂层。同样重要的是要注意所获得的 Al2O3 基体是致密且烧结良好的,没有观察到孔隙,如图 4b 所示。这是由于形成了密集的颗粒状 Al2O3 纳米颗粒 (150 nm),它具有良好的烧结能力,证明了这项工作的新技术。使用 3 点弯曲试验获得的 CNP-Al2O3 复合材料的弹性模量绘制为 Al2O3 粒径和表面覆盖百分比的函数如图 5 所示。从图 5a 中,使用制造的样品的表现出的弹性模量Al2O3 颗粒只有大约 390 GPa,这与在 300 和 400 GPa 之间的多晶 Al2O3 报道的结果一致 [6, 12]。该弹性模量值的实现证实了 SEM 观察,其中使用粒状 Al2O3 纳米粒子实现了良好的微观结构和压实。在足冢等人的研究中。关于孔隙率对氧化铝陶瓷力学性能的影响,没有孔隙率的陶瓷(0%)的弹性模量略低,约为 380 GPa [17]。至于 CNP-Al2O3 复合材料的弹性模量,可以看出,随着 CNP 体积百分比添加量的增加或 Al2O3 粒径的增加,该特性可以得到控制,因为它会线性降低。在 Shin 等人的工作中也观察到了类似的趋势,他们的还原氧化石墨烯和单壁 CNT-氧化铝复合材料的弹性模量通过增加添加剂含量而降低 [6]。由于这两个因素(CNP 的量和 Al2O3 的粒径)都对比表面积有很大的影响,导致 CNP 在 Al2O3 颗粒表面上的吸附更大,这将抑制 Al2O3 的烧结,并可能导致碳层的滑移效应较低的弹性模块 [6]。这一发现与 Gopalan 等人报道的一致。其中复合材料中使用的 CNT 延缓了晶粒生长,但对晶界滑动没有影响,从而导致超塑性的发生 [15]。这一发现表明,通过设计用于形成 CNP-Al2O3 的前体复合材料来控制微观结构的形成,可以改变和控制 Al2O3 陶瓷的弹性模量。在图 5b 中,显示了所获得的弹性模量与 Al2O3 上 CNP 覆盖率的函数关系图。观察到 CNP 覆盖率和弹性模量强度之间的线性相关性,这进一步证实了上述结果。因此,这些结果表明,CNP-Al2O3 复合陶瓷的机械性能可以通过改变 CNP 添加量或初级 Al2O3 的粒径来控制 CNP 覆盖率。在测定 CNP-Al2O3 复合样品的显微硬度时,对纯 Al2O3 和添加 1.0 vol% CNP 制备的 CNP-Al2O3 样品进行了比较,该样品具有不同的 Al2O3 粒径,分别为 37、62 和 98 μm。得到的压痕结果如图 6 所示。得到的结果表明,纯氧化铝样品表现出最高的硬度值,而 CNP-Al2O3 复合样品的硬度随着 Al2O3 粒径的增大而降低。这是因为当颗粒尺寸增加导致更多的 CNP 吸附在表面时,Al2O3 的总表面积较低。随后,由于抑制了 Al2O3 界面之间的有效烧结或沿 Al2O3 晶界的连续连接碳层的滑移,Al2O3 界面上较高量的 CNP 导致硬度降低。因此,控制 CNP 在 Al2O3 表面的分布至关重要,以诱导形成所需的微观结构,从而获得所需的 CNP-Al2O3 复合材料的机械性能。
<图片>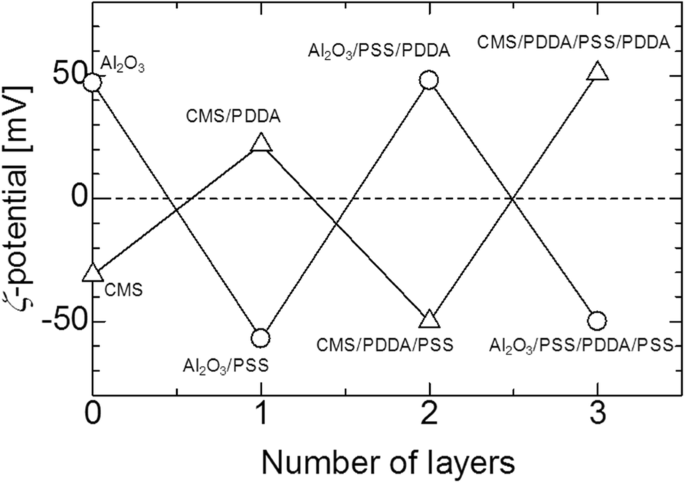
表面电荷控制的Al2O3和碳纳米粒子的Zeta电位
图> <图片>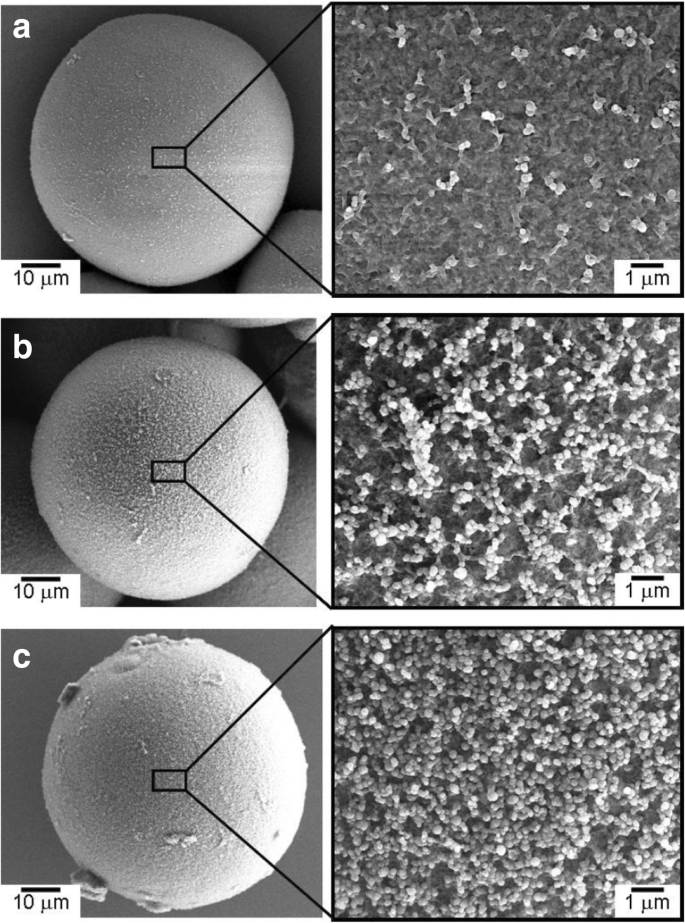
a 的 SEM 图像 0.3 vol%,b 0.6 vol% 和 c 1.0 vol% CNP包覆在平均粒径为62 μm的Al2O3造粒颗粒上
图> <图片>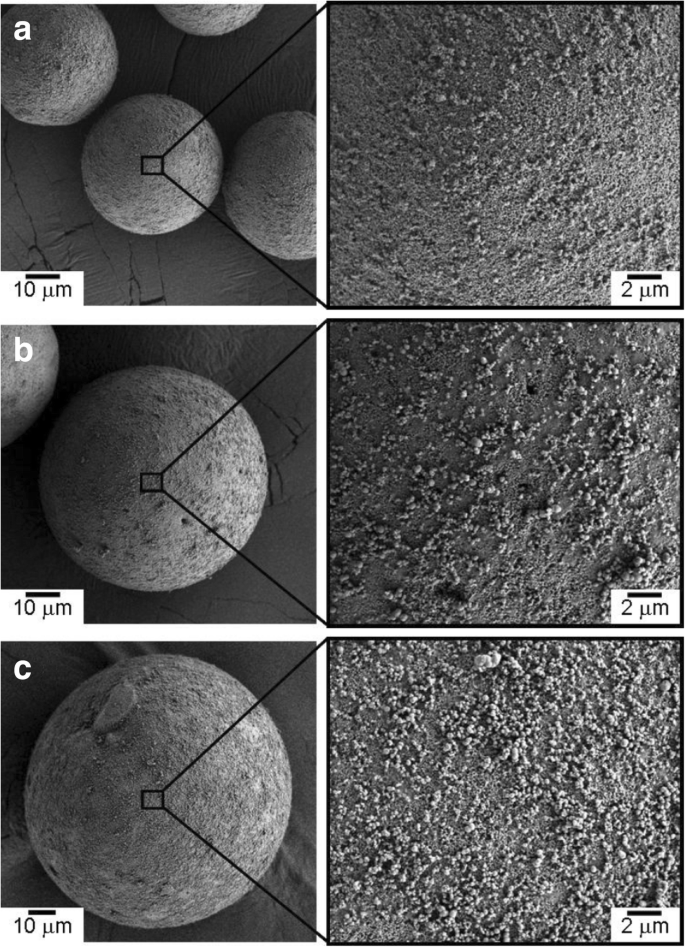
平均直径为a的Al2O3造粒颗粒上包覆0.6 vol%CNP的SEM图像 37、b 62 和 c 98 μm
图> <图片>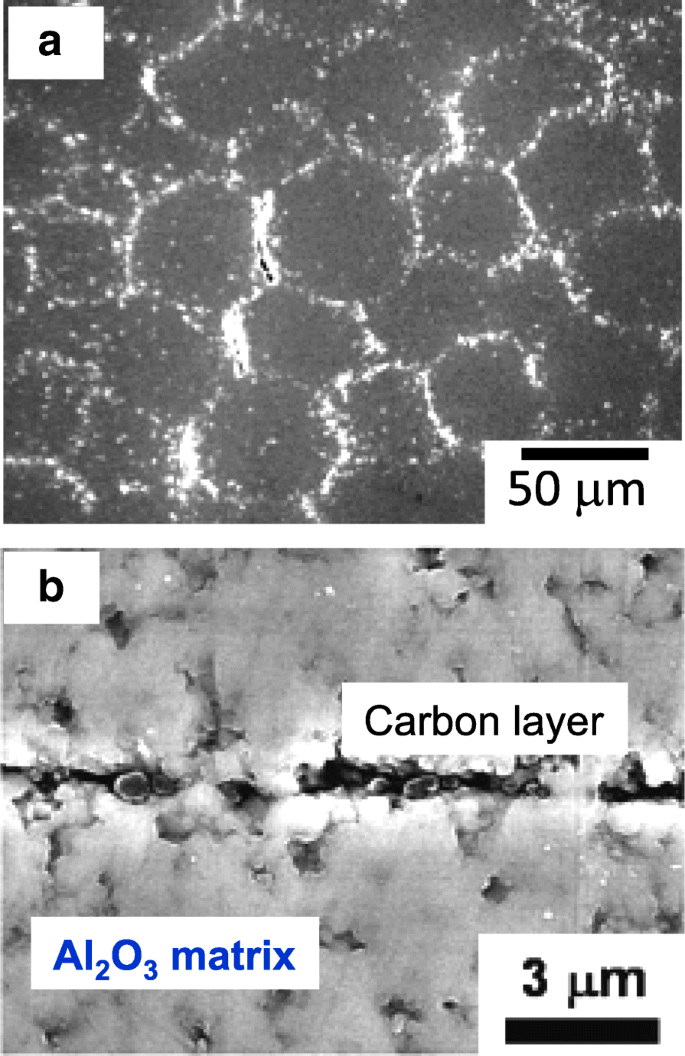
一 使用平均直径为 62 μm 的 Al2O3 制成的 0.6 vol% CNP-Al2O3 复合材料的微观结构。 b CNP-Al2O3 复合材料的晶界。在Al2O3基体界面处可观察到碳层
图> <图片>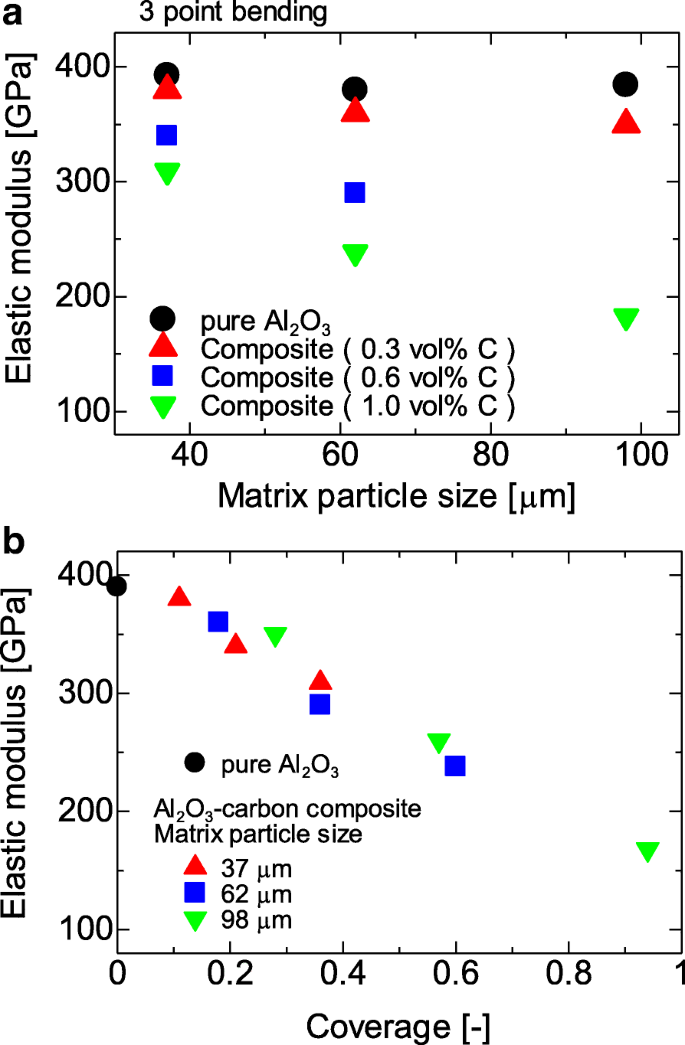
CNP-Al2O3 复合材料的弹性模量作为 a 的函数 基质粒径和b CNP覆盖Al2O3颗粒
图> <图片>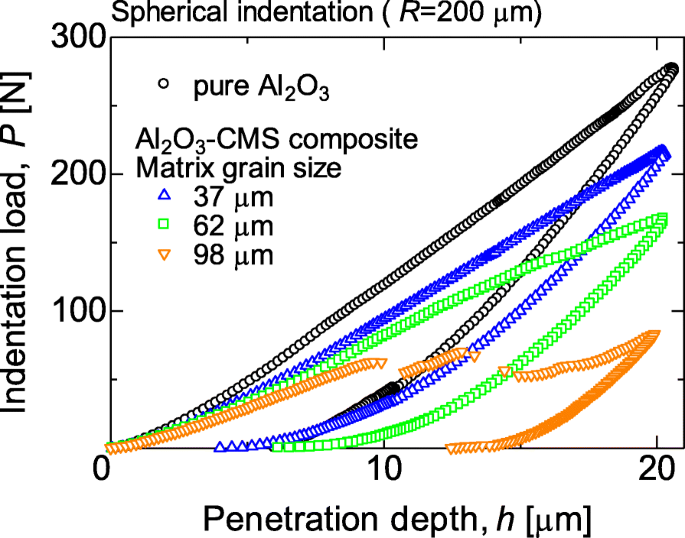
1.0 vol% CNP-Al2O3复合材料压痕载荷与穿透深度滞后曲线
图>从压痕载荷 (P )-深度 (h ) 曲线 (P -h 曲线)在加载和卸载循环过程中,可以获得微观结构变化和表面变形机制[18]。涉及压痕载荷的简单二次方程 (P ) 和穿透深度 (h ) 所示。 2可用于加载过程的分析[18,19,20]。
$$ P\propto {h}^2 $$ (2)单片 Al2O3 的负载证明了与 P 的相关性 -h 曲线类似于二次方程。如图2所示,而使用尺寸为37和62 μm的Al2O3颗粒制备的CNP-Al2O3复合材料分别表现出与整体Al2O3加载曲线的线性和偏离曲线。这表明微结构内存在 CNP(在晶界界面),导致沿晶界的局部变形。对于使用粒径为 98 μm 的 Al2O3 制备的 CNP-Al2O3 复合材料,晶界处 CNP 的高密度导致 P 不连续 -h 由于晶界滑移或表面微裂纹的发生,显示出最低的硬度。
结论
在这项工作中,证明了通过静电吸附方法控制形成 CNP-Al2O3 复合材料的可行方法。所用的 Al2O3 微粒是通过将纳米尺寸 (150 nm) 的 Al2O3 颗粒造粒而获得的,这种颗粒具有更好的压实性和烧结能力。在复合陶瓷的形成过程中,研究了涉及 CNP 量(0.3、0.6、1.0 vol%)和初级粒状 Al2O3 微粒尺寸(37、62、92 μm)的参数。结果表明,通过控制 CNP 添加剂的量和 Al2O3 微粒尺寸,可以获得不同的表面覆盖率,从而控制具有不同机械性能的微观结构形成。使用均质的 CNP-Al2O3 复合材料,沿 Al2O3 的晶界获得了连续互连的碳层。由于 Al2O3 纳米颗粒的良好烧结,还观察到致密且致密的 Al2O3 基体。从 3 点弯曲和压痕测试的结果来看,通过调整 CNP 在 Al2O3 上的覆盖率来控制机械性能。弹性模量的变化是由于有效烧结的抑制或在 Al2O3 界面处产生的碳层的滑动。从这项研究中,我们证明了使用 CNP-Al2O3 复合材料具有互连界面的陶瓷微结构设计的可行性。这种微结构设计方法将通过自下而上的组装为材料设计开辟更大的可能性和潜力,从而为广泛的应用带来所需的性能。
数据和材料的可用性
本研究期间生成或分析的所有数据均包含在这篇已发表的文章(及其补充信息文件)中。
更改历史
缩写
- CNP:
-
碳纳米粒子
- PDDA:
-
聚二烯丙基二甲基氯化铵
- PSS:
-
聚苯乙烯磺酸钠
- SDC:
-
脱氧胆酸钠
- SEM:
-
扫描电子显微镜
纳米材料
- 树脂和纤维复合材料的特性及其有益的原因
- 富勒烯衍生纳米材料及其聚合物复合材料的顺磁特性:剧烈泵出效应
- 石墨烯和多壁碳纳米管对 Cu/Ti3SiC2/C 纳米复合材料的微观结构和机械性能的协同作用
- 使用分子束外延法制备锗铋薄膜及其光学特性
- 石墨烯/Ag3PO4 量子点复合材料的简便一步声化学合成和光催化性能
- 利用柠檬汁通过水热反应制备的荧光碳量子点的材料和光学特性
- 溶胶-凝胶改性的 pH 调节参数对纳米晶锶铁氧体的结构、微观结构和磁性的影响
- 纳米粒子和超声波控制的水过冷
- 无镉 Cu 掺杂 ZnInS/ZnS 核/壳纳米晶体:可控合成和光物理特性
- Pr2CuO4 纳米片的可控合成和选择性吸附特性:机理讨论
- 表面活性剂对分层 SnO2 开花纳米花的微观结构及其气敏特性的影响
- 工程材料的特性:一般、物理和机械