预退火电沉积纳米晶镍在轧制过程中微观结构稳定性的比较研究
摘要
微结构稳定性是纳米晶材料在许多领域实际应用的重要问题。目前的工作基于 X 射线衍射线轮廓分析和透射电子显微镜观察,展示了在预退火的电沉积纳米晶镍中,微观结构如何随轧制应变演变,其中包含初始强纤维织构。将剪切应变对金属/轧辊接触界面微观结构稳定性的影响与金属/金属接触界面进行比较;后者更接近平面应变压缩中的变形。从统计的显微组织信息,再加上最终轧制后变形晶粒的实验观察,可以得出结论,金属/金属接触界面的微观结构在压延过程中比金属/轧辊界面的微观结构更稳定。
介绍
晶粒尺寸小于 100 nm 的纳米晶 (nc) 材料通常表现出优异的机械性能,尤其是高强度和高硬度,可用于各种技术应用 [1]。然而,近年来的大量研究表明,微观结构稳定性是数控材料在实际应用中不可避免的、非常重要的问题[2,3,4]。作为最常见的微观结构特征之一,在数控材料的生产和加工过程中,晶粒尺寸总是被放在首位。不幸的是,已经发现在对 nc 材料进行热处理或机械加工时可能会出现明显的晶粒生长 [5,6,7,8,9]。对于晶粒尺寸范围从 ~ 20 到数百微米的材料,遵循经典的 Hall-Petch 关系,晶粒生长将导致性能下降或恶化。在对 nc 金属的微观结构和性能之间关系的实验研究中,通过高分辨率透射电子显微镜和/或三维原子探针获得了大量的微观结构信息 [10,11,12,13]。这些结果看似直接可见,但由于这种局部观察过于微观,难免受到质疑。因此,从更宏观或全局的角度来理解塑性变形物理是必要和重要的。
对变形 nc 材料的微观结构发展进行比较的结果表明,晶粒生长行为受初始微观结构的影响,例如晶粒取向、内应力和晶体缺陷密度 [6, 14,15,16]。因此,很难与其他文献中的微观结构演变结果进行比较。在名义上相同的变形条件下,预计两个或多个样品会同时变形。请注意,累积滚压接合是通过引入大应变和应变梯度来产生超细晶粒微观结构的强大技术之一 [17, 18]。在我们之前的研究中,包装轧制已被选为变形加工路线。已经初步探讨了压延变形对 nc Ni 的微观结构、织构和硬度的影响 [19, 20]。已经表明,具有不同晶粒尺寸的变形区经受不同的应变。但尽管如此,很少关注对微观结构演变的深入比较分析,例如晶体缺陷密度的变化。因此,本研究旨在进一步研究压延nc Ni的显微组织稳定性。
材料和方法
选择纯度为99.8%的全致密电沉积数控镍片作为本研究材料。在轧制变形之前,厚度为~ 0.22 毫米的原样首先在真空中在 373 K 下退火 30 分钟以释放残余应力。没有发现明显的晶粒生长的证据。随后,将预退火的板切成尺寸为 6mm × 5mm 的小块。通过 X 射线衍射 (XRD) 分析选择具有名义上相似的初始微观结构的两块样品堆叠在一起,然后在室温下通过一对直径为 180 毫米的辊。每次轧制后,发现两个变形样品的厚度减少量几乎相同。在这种包装轧制过程中,每个样品的名义轧制应变由ε决定 =\( 2\ln \left({t}_0/t\right)/\sqrt{3} \), 其中 t 0 和 t 分别是初始厚度和最终厚度[21]。在这方面,我们特别关注金属/金属接触界面和金属/辊接触界面的微观结构演变。为方便起见,将金属/金属接触界面简称为M/M界面,将金属/辊接触界面简称为M/R界面。
变形引起的微观结构变化通过 XRD 分析在 Rigaku D/MAX-2500 PC 衍射仪上进行定量检查,该衍射仪具有旋转 Cu 靶(18KW),在固定时间扫描模式下运行。相关的微观结构参数,如晶粒尺寸和微应变,是通过 X 射线衍射线轮廓分析获得的 [22, 23]。为了验证XRD结果,采用透射电子显微镜(TEM)对法向-轧制方向截面的最终微观结构,特别是晶粒尺寸分布进行了直观的评估。通过在甲醇和硝酸 (V :V =4:1) 在 243 K 的温度下。在 ZEISS LIBRA 200FE 上在 200 kV 的加速电压下进行 TEM 观察。在明场成像中观察到晶粒形态。相应地使用暗场成像进行晶粒尺寸测量。对于每个样品,测量了 200 多个晶粒以捕捉晶粒尺寸分布的整体演变。此外,考虑到小试样的尺寸有限,在每道次轧制后,使用HVS-1000显微维氏硬度计在0.196 N载荷下对试样两侧进行显微硬度测量。
结果和讨论
图 1 显示了具有不同轧制应变的复合轧制 nc Ni 样品的 M/R 和 M/M 界面的典型 XRD 图案。对于退火态的未变形样品 (ε =0),M/R界面与M/M界面的衍射强度无显着差异。对织构系数的进一步分析表明,未变形样品具有初始强的纤维织构。正如预期的那样,衍射强度,特别是对于(111)和(200)峰,在多次压延变形(ε =0.25 和 ε =0.50)。根据先前涉及变形织构发展的研究,界面 M/R 以剪切变形为主,而界面 M/M 更接近于平面应变压缩中的变形 [24,25,26]。对(111)和(200)峰的归一化结果进行定量分析,证明界面M/R与界面M/M存在一定的差异。在 M/R 界面的情况下,衍射峰明显变窄,这主要是由于变形引起的晶粒长大。然而,在M/M界面的情况下,观察到明显的峰展宽和峰移,表明在轧制过程中产生了大量的位错和堆垛层错等晶体缺陷。
<图片>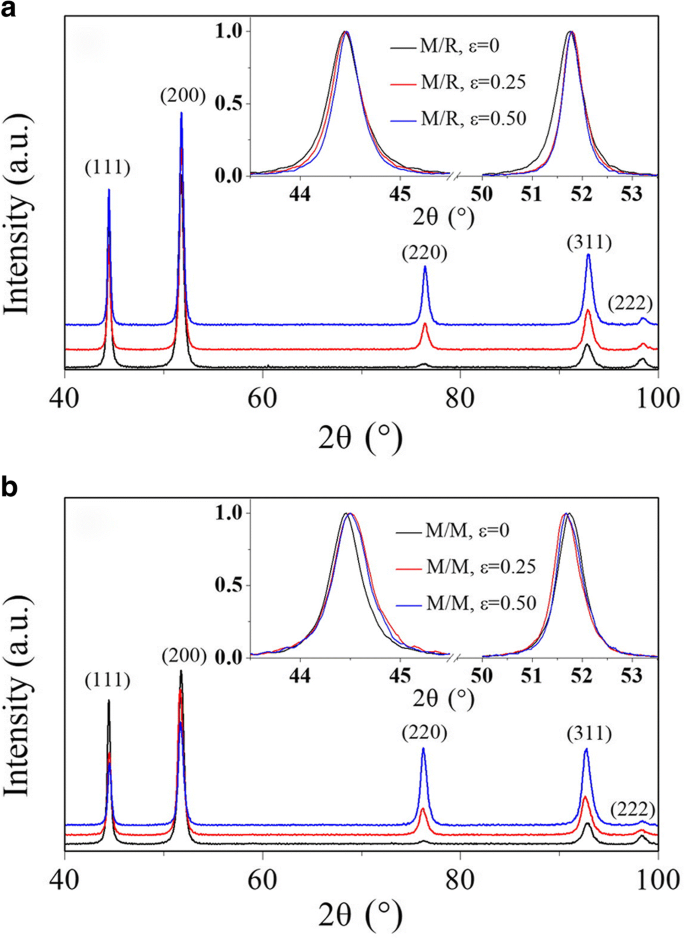
a的典型XRD图 金属/辊 (M/R) 接触界面和 b 预退火电沉积纳米晶镍在压延变形过程中的金属/金属 (M/M) 接触界面。 (111)和(200)反射面的归一化峰显示在右上角
图>图 2 显示了每次轧制后 nc Ni 的半定量结果,由 X 射线衍射线轮廓分析确定。通过峰移评估的整体堆垛层错概率 (SFP) 如图 2a 所示。对于界面 M/M,随着应变的增加,整体 SFP 呈现出相对稳定的上升趋势。然而,对于界面 M/R,SFP 在轧制变形的早期阶段显示出急剧增加,在 ~ 0.1 的小应变下达到最大值 0.015。随后,随着连续变形,该 SFP 逐渐减小,并在应变为 0.5 时获得 0.006 的值,与 M/M 界面的 SFP 相比,该值仅为三分之一。考虑到NC金属堆垛层错的产生机制,这种差异表明不同界面的微观结构应该经历不同的演化路线。
<图片>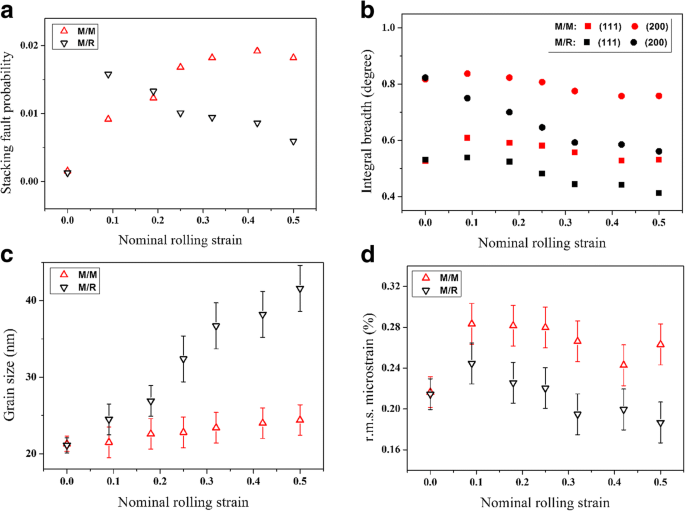
a的定量结果 堆垛层错概率,b (111) 和 (200) 峰的积分宽度,c 晶粒大小和 d r.m.s. X射线衍射线剖面分析得到的微应变
图>图 2b 显示了 (111) 和 (200) 峰积分宽度的变化。可以看出,在整个压延变形过程中,M/M界面的两个衍射峰的积分宽度明显高于M/R界面。特别值得注意的是,当将最终变形状态与退火状态进行比较时,界面 M/M 的积分宽度没有大的变化。鉴于此,从 XRD 线轮廓分析中仔细研究了晶粒尺寸和均方根 (r.m.s.) 微应变的演变。从图 2c 中可以看出,变形样品的两个界面显示出晶粒粗化的趋势,但粗化速率不同。位于 M/R 界面的晶粒平均尺寸增加得更快,这由以下 TEM 观察证明。另一方面,微应变分析表明 r.m.s. 有小幅增加。轧制变形早期两个界面的微应变,如图 2d 所示。随着变形的继续,r.m.s.界面内的微应变 M/R 开始稳步下降并稳定在 ~ 0.19% 的水平,而 r.m.s.界面内的微应变 M/M 趋向于稳定在 ~ 0.26% 的水平。 r.m.s.的这种减少微应变与先前关于大变形后冷轧电沉积 NC Ni-Fe 合金的报道一致。与晶粒尺寸演变相结合,r.m.s. 减小的主要原因。微应变与晶粒的聚结和粗化有关[27,28,29]。
图 3 显示了 M/M 和 M/R 界面的典型 TEM 结果。可以清楚地表明,变形后位于 M/R 界面的晶粒确实大于位于 M/M 界面的晶粒。对晶粒尺寸分布的进一步分析表明,未变形样品中有很大比例(超过 75%)的晶粒直径小于 40 nm。 ε之后 =0.50 轧制变形,M/R 界面小晶粒(40 nm 以下)比例明显下降。相反,大晶粒(大于 50 纳米)的比例会增加。基于先前对变形晶粒中位错活动的研究,全位错将逐渐开始主导大晶粒的变形[30,31,32,33]。因此,不难理解,M/M 接口的 SFP 远高于 M/R 接口的 SFP。
<图片>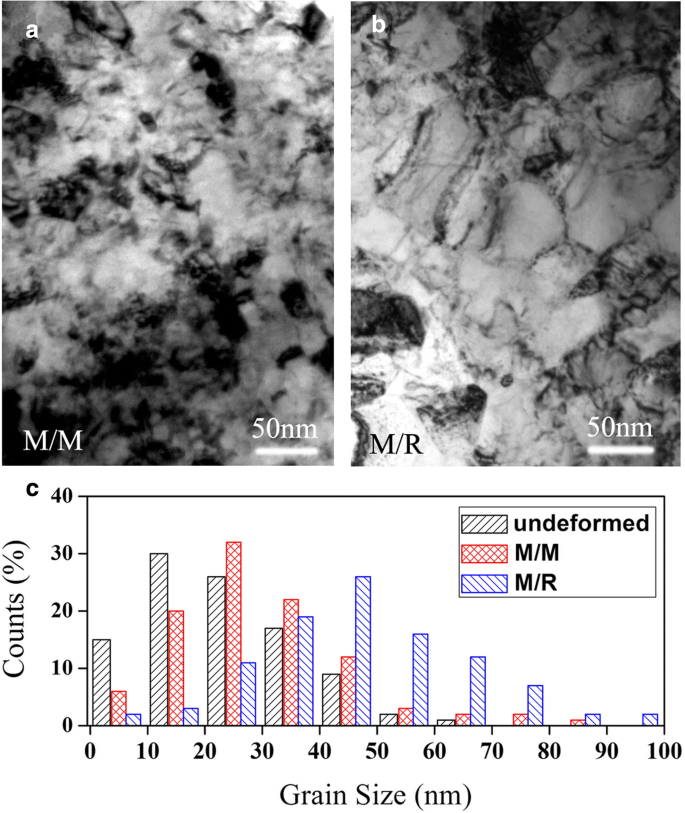
a 的典型 TEM 图像 金属/金属 (M/M) 接触界面和 b 最终包装轧制道次后的金属/轧辊 (M/R) 接触界面。变形前后的晶粒度分布如图c
图>为了将微观结构演变与机械响应相关联,M/M 和 M/R 界面的显微硬度变化如图 4 所示。在变形早期,两个界面之间没有明显差异。随着应变的增加,M/M界面的显微硬度不断增加,但M/R界面的显微硬度出现下降。另一方面,与退火态样品的晶粒尺寸和显微硬度相比,尽管存在晶粒粗化,但变形诱导应变硬化发生在 M/M 和 M/R 界面。根据经典的 Hall-Petch 关系,显微硬度会随着晶粒尺寸的增加而降低。因此,对于变形后的样品,考虑了 Bailey-Hirsch 关系 [34, 35]。探讨了显微硬度与位错密度的平方根的关系。发现偏离 Bailey-Hirsch 行为也就不足为奇了。在变形后期,残余位错密度由 r.m.s. 决定。显微应变略低于 M/R 界面的退火状态,但相应的显微硬度略高。在此,基于获得的宏观区域对应的显微组织信息,尝试探究位错密度和晶粒尺寸这两个常见的显微组织因素对显微硬度的贡献。取 nc Ni [36,37,38] 的报告值或计算值,显微硬度的估计值也显示在图 4 中。总体而言,界面 M/M 的估计值高于界面 M/R,间接表明微观结构演化的统计 XRD 结果是可信的。此外,通过对估计值和测量值之间差距的综合比较和分析,可以得出结论,变形的nc样品内部应该存在另一种强化机制,例如位错-位错相互作用[37]。特别是M/R界面,大晶粒内可能存在位错-位错相互作用,有助于提高加工硬化程度。
<图片>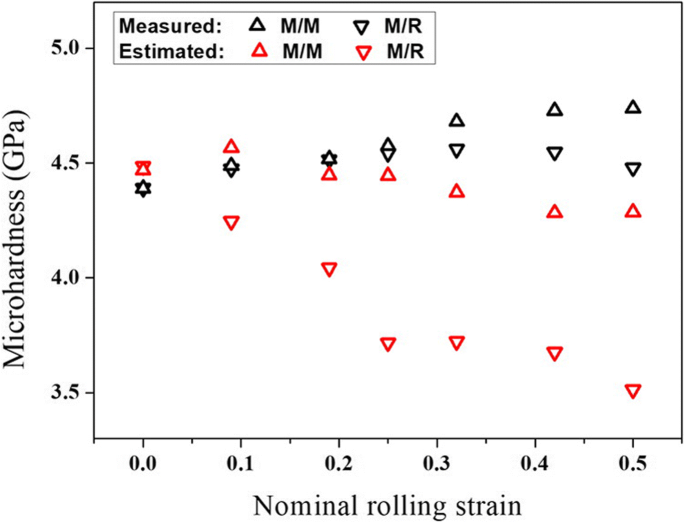
预退火纳米晶镍包轧过程中显微硬度演变的实验测量和估计预测。基于Hall-Petch关系和Bailey-Hirsch关系,显微硬度的估计值仅由晶粒尺寸和位错密度决定
图>结论
在这项工作中,基于 X 射线衍射线轮廓分析,定量研究了纳米晶镍在压延变形过程中的微观结构稳定性。通过透射电镜观察和显微硬度测量验证了一些相关结果的可靠性。金属/金属接触界面和金属/辊接触界面之间微观结构发展的差异尤其值得关注。结果表明,由于外加应变不同,两个界面的微观结构经历了不同的演化路线。从晶体缺陷密度和晶粒尺寸等微观结构统计信息可以得出结论,金属/金属接触界面在压延过程中的微观结构比金属/轧辊界面的微观结构更稳定。
缩写
- 月/月:
-
金属/金属
- M/R:
-
金属/卷
- nc:
-
纳米晶
- r.m.s.:
-
均方根
- SFP:
-
堆垛层错概率
- TEM:
-
透射电子显微镜
- XRD:
-
X射线衍射
纳米材料