用于直接甲醇燃料电池应用的各种碳载体和导电聚合物上的铂基催化剂:综述
摘要
铂 (Pt) 基纳米颗粒金属受到了大量关注,是直接甲醇燃料电池 (DMFC) 最受欢迎的催化剂。然而,Pt 催化剂的高成本、缓慢的动力学氧化以及在甲醇氧化反应 (MOR) 期间形成 CO 中间分子是与单金属 Pt 催化剂相关的主要挑战。最近的研究集中在使用 Pt 合金,如 Fe、Ni、Co、Rh、Ru、Co 和 Sn 金属或碳载体材料来提高 Pt 的催化性能。近年来,负载在具有巨大潜力的碳材料如 MWCNT、CNF、CNT、CNC、CMS、CNT、CB 和石墨烯上的 Pt 和 Pt 合金催化剂因其显着的特性而受到了极大的关注,这些特性有助于实现优异的 MOR和 DMFC 性能。本综述总结了上述合金和载体材料的发展,这些合金和载体材料与减少 Pt 的使用、提高稳定性和更好的 Pt 在 DMFC 中的电催化性能有关。最后,从形貌、电催化活性、结构特征和燃料电池性能方面对每种催化剂和载体进行了讨论。
介绍
燃料电池技术在世界范围内受到广泛关注。燃料电池 (FC) 是一种很有前景的替代发电技术,可通过电化学反应将化学能转化为电能 [1, 2]。此外,对于燃料电池技术,燃料电池技术的主要重点是实现低成本生产,从而实现燃料电池系统的强大性能并发现耐用材料。然而,当前燃料电池技术中出现的常见问题是这些系统涉及高内在成本和较差的耐用性 [1]。尽管它有望成为燃料电池,但直接甲醇燃料电池 (DMFC) 仍存在挑战和局限性,这促使研究人员研究提高 DMFC 效率和性能的方法。 DMFC 的许多问题已被确定但仍未解决,包括甲醇燃料从阳极电极到阴极电极的交叉 [3,4,5] 由缓慢的动力学速率、催化剂的不稳定以及热和水管理引起的性能不佳[6,7,8]。
近年来,对燃料电池进行了大量研究,包括DMFC、质子交换膜燃料电池(PEMFC)、固体氧化物燃料电池(SOFC)等,这些都是流行的燃料电池技术。作为一种新型能源,DMFC 可用于移动和固定应用 [9, 10]。燃料电池领域已取得多项研究进展。在燃料电池中,DMFCs 因其高功率密度、易于燃料处理、易于充电和低环境污染等诸多优点,近年来得到了广泛的研究 [11,12,13,14,15,16]。影响 [17, 18]。然而,DMFC 商业化的几个技术挑战仍未解决,包括甲醇交叉、低化学反应速率和催化剂中毒。然而,DMFC 仍然受到许多研究人员的关注,并因其低温运行(DMFC 系统在 373 K 下运行)而成为最受欢迎的燃料电池。由于 DMFC 具有高能效和快速启动系统的优势,DMFC 技术非常适合用作住宅电源、移动设备中的电池和车辆燃料 [19,20,21,22]。此外,可以进一步研究 DMFC 的概念,以寻找替代燃料来源,如天然气和生物质,以及农产品发酵生产乙醇,以尽量减少对不安全能源的依赖 [14]。
在 DMFC 中,阳极侧供应甲醇溶液,通过以下反应将其电氧化为二氧化碳 (CO2):
$$ {\mathrm{CH}}_3\mathrm{OH}+{\mathrm{H}}_2\to {\mathrm{CO}}_2+6{\mathrm{H}}^{+}+6{ \mathrm{e}}^{\hbox{-} } $$ (1)而在阴极侧的质子,氧气(来自空气)被还原为水:
$$ 3/2\ {\mathrm{O}}_2+6{\mathrm{H}}^{+}+6\ {\mathrm{e}}^{\hbox{-}}\to 3{\ mathrm{H}}_2\mathrm{O} $$ (2)DMFC反应的净方程式可概括如下:
$$ {\mathrm{CH}}_3\mathrm{OH}+3/2{\mathrm{O}}_2\to {\mathrm{CO}}_2+2{\mathrm{H}}_2\mathrm{ O} $$ (3)在 DMFC 系统中,有两种类型的 DMFC 模式:主动模式和被动模式 [23,24,25]。在主动 DMFC 系统中,DMFC 烟囱的出口流通过液态甲醇进料的闭环控制进行再循环。同时,阳极流中的液态甲醇由甲醇浓度传感器控制,该传感器在提供足够的额外甲醇和水注入以根据目标浓度恢复该燃料方面发挥重要作用。 DMFC 系统中使用了多种类型的甲醇浓度传感器来控制和维持甲醇进料浓度 [17]。通常,液态甲醇通过蠕动泵输送到阳极侧,而周围的含氧空气通过鼓风机或风扇输送到阴极侧 [16]。在被动模式的 DMFC 系统中,液态甲醇连续供入系统。这种被动概念对 DMFC 系统非常有吸引力 [26,27,28]。被动的概念意味着系统完全自主运行,无需任何支持设备。被动 DMFC 的概念意味着该系统完全自主运行,无需任何外部设备的帮助来泵送甲醇和将空气吹入烟囱。在 DMFC 系统的被动模式下,催化剂层将由作为反应物的甲醇和氧气供应。在甲醇氧化反应 (MOR) 期间,CO2 和水将通过被动方式从电池中去除,即扩散、自然对流、毛细管作用等 [20]。与主动模式 DMFC 相比,被动模式 DMFC 在更简单、更紧凑的设计和低成本方面似乎更具优势。复杂的系统设计和控制可能是主动模式 DMFC [21] 的一个缺点。从实际用途来看,主动模式DMFC似乎更适合高功率系统,而被动模式DMFC更适合低功耗需求[22]。
图 1 显示了单电池 DMFC 的设置和设计。单电池 DMFC 堆由夹在两块阳极和阴极板之间的五层膜电极组件 (MEA) 组成。在阳极侧,液态甲醇(含有甲醇和去离子水)和无水甲醇通过蠕动泵流入通道。在阴极侧,空气通过转子流量计泵入燃料电池。 DMFC电堆中的温度控制器通过辅助加热装置维持电池的工作温度。电子负载装置用于改变电流密度到不同的水平并测量相应的电压值。电池性能由电化学工作站监控,而作为整个反应最终产物的 CO2 的产生由 CO2 浓度检测器测量 [23]。在直接甲醇燃料电池中,在实验研究期间必须考虑几个重要的操作参数,它们是 (i) 工作温度,(ii) 甲醇浓度,以及 (iii) 进料甲醇溶液和空气的输入流速 [23] .图 2a、b 分别显示了 DMFC 的主动和被动模式。
<图片>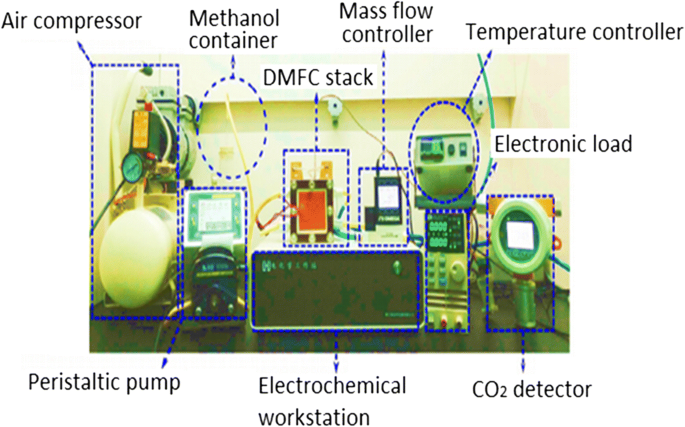
单细胞DMFC的通用实验装置[23]
图> <图片>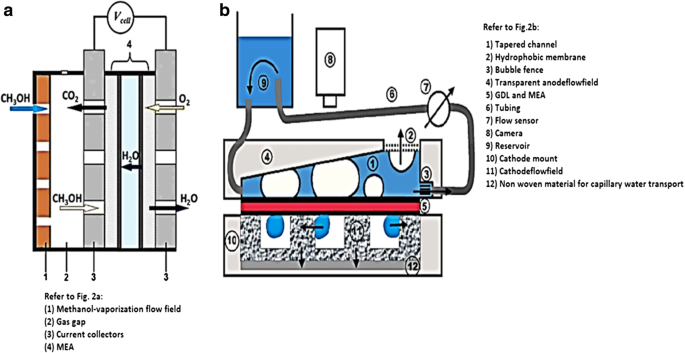
a示意图 主动模式 [24] 和 b DMFC的被动模式[25]
图>本综述将重点介绍基于 Pt 催化剂作为 DMFC 贵重催化剂的催化剂载体的研究和开发的最新进展。我们将铂基催化剂与合金、金属、过渡金属、金属碳化物、金属氮化物和各种含碳物质(如石墨烯/氧化石墨烯 (G/GO)、碳纳米管 (CNT)、碳纳米纤维 ( CNF)、碳纳米线圈 (CNC)、炭黑 (CB)、多壁碳纳米管 (MWCNT) 和碳介孔 (CMS) 载体,以及作为载体的聚苯胺 (PANi) 和聚吡咯 (Ppy) 等导电聚合物材料。许多合成方法可用于制备 Pt 基催化剂。用于获得纳米级 Pt 颗粒的最常用方法是浸渍 [29,30,31,32,33,34]、水热技术 [35,36,37,38,39,40,41]、微乳液 [42,43, 44,45] 和减少 [46, 47]。一般来说,制备方法会影响催化剂颗粒的形貌和尺寸;因此,催化剂合成方法的选择十分重要。
各种铂基催化剂的性能
在过去的十年中,许多研究人员将研究重点放在电催化剂的开发上,以提高其在甲醇 MOR 中的 DMFC 系统电催化活性 [37, 38]。铂 (Pt) 是一种单金属催化剂,对 MOR 显示出非常高的催化活性。然而,DMFC 系统中单独使用纯 Pt 可能容易被中间物种即一氧化碳 (CO) 中毒,并且 Pt 催化剂的高成本限制了其作为电催化剂的商业应用,从而降低了甲醇氧化的动力学速率在 DMFC 系统中 [48,49,50]。这三点是单独使用 Pt 作为 DMFC 电催化剂的主要障碍和限制。然而,为了克服这些障碍,已经进行了几项研究来合成 Pt 基合金电催化剂,以在使用较少的 Pt 的情况下获得更好的电催化性能 [11, 47, 51, 52]。通常,Pt 粒子的平均尺寸及其形貌可以通过扫描发射显微照片 (SEM) 或透射电子显微照片 (TEM) 分析来确定,这是催化领域最常用的方法,可用于表征电催化剂的物理性质。表1显示了不同合成方法、性质和性能的Pt粒子的平均粒径。
图>由于其双功能机制和配体效应,双金属 PtRu 被认为是最活跃的催化剂 [48, 53]。 PtRu 成为一种有趣的催化剂合金,直到今天一直用于许多碳载体。然而,添加钌 (Ru) 金属的毒理学影响仍不确定 [49]。因此,已对将 Pt 与其他非贵金属混合的较便宜的合金进行了研究 [49,50,51,52, 54,55,56,57],如“Pt 基合金的性能”部分所述。>
铂基合金的性能
阿里科等人。 [35] 发现已经进行了大量研究以提高 MOR 中 Pt 催化剂的催化活性。在许多研究中,最佳 Pt-Ru 比例已确定为 1:1,纳米级的粒径是提高催化剂利用率的理想尺寸。然而,石等人。 [38] 在他们的实验中确定 3:2 是 Pt-Ru 的最佳比例,以提高 MOR 催化活性。除此之外,如果 PtRu 电催化剂颗粒是 2-4 nm 范围内的纳米级颗粒,也可以提高甲醇电氧化活性的电催化活性。保拉斯等人。 [39] 同意这一说法。众所周知,Pt 对甲醇燃料显示出高反应性,这使得 Pt 金属成为 DMFC 系统中阳极电极的理想电催化剂。然而,在 Pt 催化剂的 MOR 过程中,一氧化碳 (CO),即中间物质,将在 Pt 颗粒表面形成,从而使催化剂表面中毒 [58,59,60,61]。因此,需要一些努力来克服与在 Pt 颗粒表面形成有毒物质有关的问题,以便它们不会覆盖 Pt 的活性位点区域。一般而言,二元合金,如PtRu [62,63,64,65,66], PtRh [67,68,69,70,71], PtAu [72,73,74], PtSn [62,63,75, 76,77]、PtNi [64,65,66,67,78,69]、PtCo [70, 71, 78,79,80] 和 PtFe [81,82,83,84,85] 经常被使用作为 DMFC 系统中阳极电极的电催化剂组合。添加这些金属,如钌(Ru)、锡(Sn)和铑(Rh),被认为会产生更高的催化活性。
将镍 (Ni) 加入铂基催化剂可为 MOR 和 DMFC 提供卓越的性能。在最新研究中,Guerrero-Ortega 及其同事解释说,在 Pt-Vulcan 载体中添加 Ni 会促进 MOR 期间法拉第电流的重要增加一个数量级,即使双金属催化剂中 Pt 的使用量较低 [ 55]。他们的实验结果还表明,Ni 的加入促进了一些结构和电子的改变,从而提高了电极界面的反应性能。在另一项工作中,由于电子结构的变化和电化学活性区域 (ECSA) 的改善,将 Au 掺入 Pt 合金增强了电催化活性 [47]。同时,在 Pt 基合金中添加锡 (Sn) 显示出电催化活性的增加,这受到合金体系中 Sn 掺入和氧化形式的强烈影响,由于较低的氧化电位,更容易促进反应。 56]。此外,通过 PtCo (1:9)/rGO 催化剂向 Pt 基合金中添加钴 (Co) 大大提高了催化性能,发现其比 Pt/rGO 高 10 倍 [51]。电流密度的增加归因于 PtCo 纳米颗粒在 rGO 载体的亲水性上的更高分散,这促进了水的活化并导致氧化 Pt 位点上的 COad。此外,根据 Co 的双功能机制,它促进 H2O 活化,产生更多的 -OH 离子和其他含 O2 的物质,以氧化 Pt 位点上的 CO-中间体物质 [57]。 Co 的这种双功能机制也可用于其他催化 MOR 的过渡金属。 PtCo催化剂存在下CO物种催化氧化为CO2的机理总结如下:
$$ \mathrm{Pt}+{\mathrm{CH}}_3\mathrm{OH}\to \mathrm{Pt}\hbox{-} {\mathrm{CO}}_{\mathrm{ads}}+4 {\mathrm{H}}^{+}+4{\mathrm{e}}^{\hbox{-} } $$ (4) $$ \mathrm{Co}+{\mathrm{H}}_2\ mathrm{O}\to \mathrm{Co}{\left(\mathrm{OH}\right)}_{\mathrm{ads}}+{\mathrm{H}}^{+}+{\mathrm{e }}^{\hbox{-} } $$ (5) $$ {\mathrm{PtCO}}_{\mathrm{ads}}+\mathrm{Co}{\left(\mathrm{OH}\right) }_{\mathrm{ads}}/{\mathrm{CO}}_2+\mathrm{Pt}+\mathrm{Co}+{\mathrm{H}}^{+}+{\mathrm{e}}^ {\hbox{-} } $$ (6)此外,Löffler 等人。 [86] 成功合成了 PtRu 作为 DMFC 的阳极催化剂,通过它在大约 50 at.% Ru 下产生了最活跃的甲醇电氧化电催化剂。与此同时,Dinh 等人。报道 [87] 比例为 1:1 的 PtRu 对甲醇氧化 (MOR) 具有更强的金属行为和更高的电催化活性。性能与这两个主要因素有关:(i) 最大化的催化剂表面积和 (ii) 具有最大数量的原子比接近 1:1 的金属合金位点的催化剂表面。这两个小组也表现出高度。基于双功能机制,Aricò 等人。 [58] 和 Goodenough 等人。 [62] 表明在 Pt 表面活性位点上形成的 CO 中间物种可以在较低电位下被次级元素(例如 Ru、Sn 和 Mo)上形成的活性氧原子氧化成二氧化碳 (CO2)地区。表 1 总结了研究人员为 MOR 进行的各种类型 Pt 合金催化剂的性能。根据双功能机制 [88,89,90],负载 PtRu 合金催化剂上的 MOR 可以总结为以下等式。 Pt 是比 Ru 更活跃的甲醇吸附催化剂。因此,PtRu电催化剂用于甲醇氧化反应的整体反应遵循双功能机制。
$$ \mathrm{Pt}+{\mathrm{CH}}_3\mathrm{OH}\to \mathrm{Pt}\hbox{-} {\mathrm{CH}}_3\mathrm{OH}\mathrm{ads }\to \mathrm{Pt}\hbox{-} {\mathrm{CO}\mathrm{H}}_{\mathrm{ads}}\to 3\mathrm{H}+3\mathrm{e}\hbox {-} \to \mathrm{Pt}\hbox{-} {\mathrm{CO}}_{\mathrm{ads}}+{\mathrm{H}}^{+}+{\mathrm{e}} ^{\hbox{-} } $$ (7) $$ \mathrm{Ru}+{\mathrm{H}}_2\mathrm{O}\to \mathrm{Ru}\hbox{-} {\mathrm{ OH}}_{\mathrm{ads}}+{\mathrm{H}}^{+}+{\mathrm{e}}^{\hbox{-} } $$ (8) $$ \mathrm{Pt }\hbox{-} {\mathrm{CO}\mathrm{H}}_{\mathrm{ads}}+\mathrm{Ru}\hbox{-} {\mathrm{OH}}_{\mathrm{ads }}\to \mathrm{Pt}+\mathrm{Ru}+{\mathrm{CO}}_{2+}2{\mathrm{H}}^{+}+2{\mathrm{e}}^ {\hbox{-} } $$ (9) $$ \mathrm{Pt}\hbox{-} {\mathrm{CO}}_{\mathrm{ads}}+\mathrm{Ru}\hbox{-} {\mathrm{OH}}_{\mathrm{ads}}\to \mathrm{Pt}+\mathrm{Ru}+{\mathrm{CO}}_2+{\mathrm{H}}^{+}+{ \mathrm{e}}^{\hbox{-} } $$ (10)参考这种双功能机制,甲醇最初解离并吸附在 Pt 上,随后通过脱氢反应分解为 COads 和/或甲酰基类物质 -CHOads (7)。同时,水分解为 OHads 并吸附在 Ru 位点上 (8)。然后物质吸附在 Pt 和 Ru 位点上并结合在一起形成 CO2 分子 (9) 和 (10)。 Pt-COads 和 Ru-OHads 之间的反应导致 CO2 释放,产生更新的 Pt 和 Ru 位点(反应 10)。而 Ewelina Urbanczyk 等人完成的另一项工作。 [48] 在碱性介质(1.0 M KOH)中对 PtNi 催化剂进行了甲醇氧化反应。理论上,甲醇在碱性介质中的氧化反应为:
$$ {\mathrm{CH}}_3\mathrm{OH}+6\mathrm{OH}\to {\mathrm{CO}}_2+5{\mathrm{H}}_2\mathrm{O}+6{ \mathrm{e}}^{\hbox{-} } $$反应在 DMFC 的 Pt 电极处开始生成二氧化碳。在此过程中,可能会形成中间分子 (CO),从而导致 Pt 活性侧中毒和失活。这种 CO 分子是甲醇不完全氧化的产物。不完全的甲醇氧化形成 CO 作为中间产物(方程式 11)。电催化剂表面也可以吸附羟基(方程式 6)。最后,由于主要产品的解吸,形成了二氧化碳 (13)。甲醇氧化过程中可能产生的第二种毒物是甲烷。在这种情况下,会发生以下反应 (8)。电化学反应中碳的中间体完全氧化为二氧化碳的过程如下:
$$ 3\mathrm{Pt}+{\mathrm{CH}}_3\mathrm{OH}\to \mathrm{Pt}-\mathrm{COads}+4{H}^{+}+2\mathrm{Pt }+4e-+{H}^2O $$ (11) $$ \mathrm{Ni}+{H}_2O\to \mathrm{Ni}-\mathrm{OHads}+{H}^{+}+e - $$ (12) $$ \mathrm{Pt}-{\mathrm{CO}}_{\mathrm{ads}}+\mathrm{Ni}-\mathrm{OHads}\to {\mathrm{CO}} _2+{H}^{+}+\mathrm{Pt}+\mathrm{Ni}+e- $$ (13) $$ \mathrm{Pt}-{\mathrm{CH}}_3+\mathrm{Pt}- H\to 2\ \mathrm{Pt}+{\mathrm{CH}}_4 $$ (14) $$ \mathrm{Pt}-{\mathrm{CH}}_3+\mathrm{Ni}{\left(\ mathrm{OH}\right)}_2\to\mathrm{Pt}+{\mathrm{CO}}_2+\mathrm{Ni}+5{H}^{+}+5e- $$ (15)目前,研究人员仍在研究合金化技术,通过制备 Pt 的三元和四元合金来提高 Pt 基电催化剂的催化活性,如 PtRuSn [91, 92]、PtRuNi [93,94,95]、PtRuMo [70, 96] , 97]、四元 PtRuOsIr [79, 80] 和 PtRuIrSn [97, 98],因为它们在 MOR 中具有出色的行为并去除了在 Pt 表面位点形成的中间物质 (CO)。但是,在这些三元和四元催化剂中添加第三和第四金属仍然未知。此外,在生产三元和四元合金方面存在一些限制和挑战。由于金属和组成的许多可能组合,催化剂形态和催化剂组成的优化变得难以实现。然而,许多研究证明,第三、第四金属的加入显着提高了催化活性,提高了催化剂的稳定性,对甲醇电氧化和DMFC应用具有良好的CO耐受性。
齐乌瓦拉斯等人。 [99] 对 PtRuMo/C 催化剂进行了电化学测量,发现尽管所有三元催化剂对 CO 和甲醇的氧化都比二元催化剂更活跃,但与三元催化剂相比,用 H2 处理的催化剂性能提高了约 15%。在 He 中处理或未经处理的催化剂。 2012 年,胡等人。 [100] 成功合成了一种优良的双金属(PtNi)电催化剂,即中空介孔 PtNi 纳米球(HMPNN)。由于HMPNNs的独特结构和大的电化学表面积,该催化剂在MOR中表现出优异的催化性能,显着提高了Pt的利用效率。在 2016 年左右,Yang 等人完成的工作。 [101] 还研究了合成双金属 PtFe 电催化剂的反应性,他们观察到 Pt 和铁 (Fe) 金属之间的强相互作用可以降低双金属 NP 的吸附能。他们还发现,当 Pt 和 Fe 原子都在表面时,双金属 PtFe 纳米粒子更喜欢通过 Fe 原子吸附在单空位石墨烯上,因为 Fe 原子和单空位石墨烯之间的相互作用强于 Pt 原子和单空位石墨烯之间的相互作用。单空位石墨烯。图 3 说明了杨等人提出的分散在石墨烯载体上的 Pt 和 Fe 颗粒的位置。 [101].
<图片>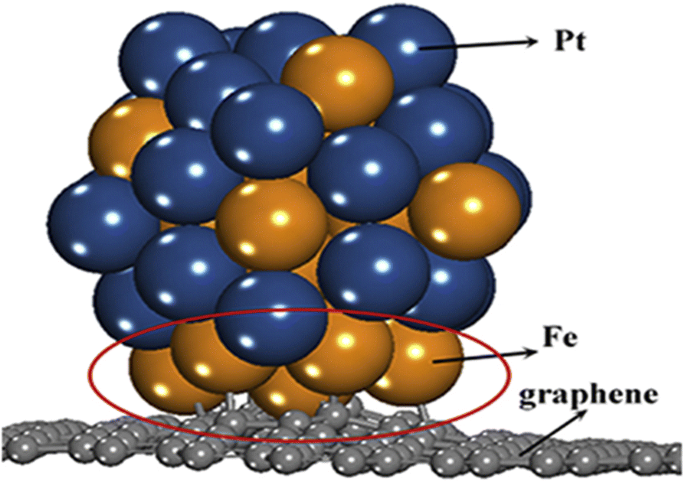
Yang等人说明了PtFe催化剂在石墨烯载体上的位置。 [101]
图>铂基催化剂和过渡金属碳化物的性能
过渡金属碳化物 (TMC) 具有抗腐蚀的高机械和化学稳定性、良好的酸性环境耐受性、长期稳定性和高 CO 耐受性,可用作阳极催化剂 [88,89,90, 102,103,104]。此外,与母金属相比,TMCs 在活性、选择性和抗毒性方面还具有许多优势,例如碳化钨 (WC) 显示出特殊性能,如良好的导电性、耐酸性环境、低成本, 以及对甲醇电氧化过程中 CO 中毒的耐受性 [88, 105, 106]。
王等人。 [103] 报道了合成高表面积 (256 m 2 g −1 ) 通过简单的水热法制备碳化钨微球。 W2C 被发现是合成样品中的主要相。目前,研究人员正在探索负载在 WC 上的 Pt 作为 DMFC 理想催化剂的潜力 [38, 88, 107, 108]。克里斯蒂安等人。 [106] 得出的结论是,相对于它们的过渡金属元素,TMCs 在某些化学和电化学反应中表现得与贵金属如 Pt、Pd、Rh 和 Ru 类似,包括氢气、一氧化碳和醇的氧化反应和氧气的还原反应[109, 110]。在另一项研究中,Liu 等人。 [107] 提出碳化钼(Mo-Carbides)可以作为碳化钨的促进剂并提高 DMFC 的电催化活性。然而,在没有加入 Pt 金属的情况下,纯 WC 对 DMFC 系统的 MOR 的电催化活性仍然很低。因此,将少量铂金属添加到 WC 组分上非常方便地获得 Pt 和 WC 之间协同效应的优势 [91, 111, 112]。与此同时,哈桑等人。 [109] 揭示了甲醇氧化过程中形成的常见杂质(CO 物种)在 Pt 表面具有很强的结合能;因此,它必须被氧化,才能从 Pt 活性位点上去除。在 Pt/WC 电催化剂中添加 WC 组分对 MOR 显示出较高的 CO 耐受性,这表明 Pt 金属和作为载体组分的 WC 之间存在协同效应。另一位研究人员也进行了这项研究,通过使用较少的 Pt 金属来降低 Pt 的成本,同时保持良好的电催化性能。
除此之外,WC 组分在形成甲氧基 (CH3O-) 方面比纯 Pt 更活跃 [113, 114]。 (Pt:Ru)4-WC/RGO 的 CV 性能表现出出色的催化性能,电流密度为 330.11 mA mg -1 Pt 与其他五种催化剂相比,表明合成的电催化剂对 MOR 具有优异的催化活性。此外,Pt催化剂上Ru和WC的结合增加了OH表面量,并使吸附在Pt表面的CO在较低电位下被氧化[39]。
铂基催化剂和过渡金属氮化物的性能
过渡金属氮化物(TMN)由于其良好的导电性(金属)、硬度、高电化学稳定性和在燃料电池运行条件下的耐腐蚀性,是作为 Pt 催化剂载体的理想候选者 [115,116,117,118]。据报道,过渡金属氮化物,如 CrsN、TiN 和 VN,与传统的碳载体相比,负载的 Pt 催化剂具有较高的催化性能和更好的稳定性[112]。除了第二和第三排第 8、9 和 10 族金属(Ru、Os、Rh、Ir、Pd 和 Pt)之外,所有过渡金属都可以形成氮化物。过渡金属氮化物的行为和结构特性可以在文献 [92,93,94] 中找到。肖等人。 [112] 制备了一种钛钴氮化物负载的 Pt 电催化剂,该催化剂对氧还原反应 (ORR) 表现出优异的性能和稳定性。 TiO.9Co0.1N负载的Pt催化剂表现出小粒径和良好的金属分散性。这种制备的电催化剂还保持了 Pt 的电化学表面积 (ECSA),并大大改善了 ECSA 的保存,在 10,000 次 ADT 循环后早期 ECSA 下降仅降低了 35%。钴掺杂显着增强了 ORR 活性和耐久性。同时,使用大表面积的 Pt(Ru)/TiN 电催化剂可以在 DMFC 系统中获得高性能和耐用的电催化剂,该电催化剂也表现出对 MOR 的高电化学活性,催化活性提高了~ 52%,并且具有良好的稳定性/耐久性。到商业 JM-Pt(Ru)。同时,DMFC 的单电池性能实现了更好的最大功率密度 56%,并表现出优异的 CSG-Pt(Ru)/TiN 电催化剂电化学稳定性[115]。
目前,Li 等人合成了负载在具有中空多孔结构和高表面积的氮化铁钛纳米管上的 Pt 纳米粒子。 [116]。它在酸性条件下对 MOR 的电催化活性显着增加,并具有更好的耐久性。这些特性的原因是由于他们的实验数据工作证实了添加 Fe 可以调整 Pt 原子的电子结构,这有助于增强 Pt 催化剂对 MOR 的活性和稳定性。同时,在肖等人之前所做的工作中。 [117],Pt/Ti0.8Mo0.2N 催化剂表现出多孔结构和高表面积、小尺寸和良好分散的 Pt 纳米粒子。该催化剂体系保留了 TiN 纳米结构的固有电化学稳定性,并显着提高了 MOR 活性和耐久性。然而,目前关于氮化钨(WN)电化学稳定性的信息仍然不足[109]。
同时,MoxN (x =1 或 2) 在 Ti 衬底上,在 4.4 M H2SO4 的酸性电解质中显示出电化学稳定性,阳极电位高达 + 0.67 V(vs. SHE),超过 50 次重复循环 [110]。然而,由于阴极和阳极腐蚀,该电催化剂在高阴极(低于 - 0.1 V vs. SHE)和阳极(高于 + 0.67 V vs. SHE)电位区域中表现出表面损伤,例如开裂和破碎。在高于 + 0.67 V(相对于 SHE)的高阳极电位区域中,由于形成 MoOx 氧化物,氧的组成增加,这可能导致失活。这些结果表明,MoxN 与水性电解质中存在的氧物质发生反应,并且在高于 + 0.67 V(相对于 SHE)时不稳定。穆斯塔法等人。 [111] 发现负载在 TiN 上作为载体的 Pt 显示出甲醇氧化的电活性,在 0.5 M CH3OH + 0.5 M 中以 20 mV/s 的扫描速率进行的伏安图中,高 If/Ib 比代表高抗 CO H2SO4 作为电解质。 Pt 和 TiN 之间的双功能效应被认为是 Pt/TiN 抗 CO 的原因。此外,Ottakam Thotiyl 等人。 [91] 对负载 Pt 的 TiN 催化剂取得了良好的效果,对甲醇的电化学氧化显示出非常好的 CO 耐受性。他们得出的结论是,TiN 的特殊特性使其适合作为碱性介质中 MOR 的 Pt 载体,因为它表现出卓越的稳定性、极强的耐腐蚀性、良好的电子导电性和强粘附行为。 TiN 负载的催化剂在长期稳定性、交换电流密度和低过电位下的稳定电流方面是有益的。实验中使用的铂负载量为 40 wt% 的 TiN。
近年来,刘等人。 [118] 在氮化钛镍装饰的 3D 碳纳米管上成功合成了铂,该纳米管通过溶剂热工艺和氮化工艺减少了氧化石墨烯 (TiNiN/CNT-rGO) 的支持。小粒径的 Pt 在 TiNiN/CNT-rGO 载体上分散良好。 The 3D shape of CNT-rGO support gives a fast route for charge transfer and mass transfer as well as TiNiN NPs with good synergistic effect and the strong electronic coupling between different domains in TiNiN/CNT-rGO support. Thus, it greatly improved the catalytic activity of this catalyst. In another research, the non-carbon TiN nanotubes-supported Pt catalyst done by Xiao et al. [119] also displayed enhanced catalytic activity and durability toward MOR compared with the commercial Pt/C (E-TEK) catalyst.
Performance of Pt-Based Catalysts with Transition Metal Oxide
Pan et al. [92] reported the synthesis of platinum–antimony-doped tin oxide nanoparticles supported on carbon black (CB) as anode catalysts in DMFC, which exhibited better improvement in catalytic activity toward MOR compared to Pt-SnO2/C or commercial Pt/C electrocatalyst. The enhancement in activity was attributed to the high electrical conductivity of Sb-doped SnO2, which induced electronic effects with the Pt catalysts. Another work done by Abida et al. [93]described the preparation of Pt/TiO2 nanotube catalysts for methanol electrooxidation. The TiO2 nanotubes-supported Pt catalyst (Pt/TiO2 nanotubes) exhibited excellent catalytic activity toward MOR and had good CO tolerance. They also reported that the use of hydrogenotitanate nanotubes as a substrate for the Pt catalyst considerably improved the COads oxidation on Pt, but the MOR still occurred at high potential. Then, several years later, Wu et al. [94] synthesized Pt-C/TiO2 with MOR activity 1.6 higher than commercial Pt-C and the stability of Pt-C/TiO2 was also enhanced by 6.7 times compared to Pt-C. The excellent performance of this catalyst was a contribution of mesopores and partially coated carbon support.周等人。 [95] prepared hollow mesoporous tungsten trioxide microspheres (HMTTS) using the spray-drying method to yield Pt/HMTTS. The electrocatalyst exhibited excellent electrocatalytic activity and high stability toward MOR than Pt/C and Pt/WO3 electrocatalysts, which may be attributed to the well-ordered Pt particles (with an average size of 5 nm) on the HMTTS surface.吴等人。 [120] used polystyrene spheres as templates to obtain pore-arrayed WO3 (p-WO3). The Pt nanoparticles with an approximate size of 3.3 nm dispersed on pore-arrayed WO3 (Pt/p-WO3) exhibited high catalytic activity toward MOR.
李等人。 [121] used Sn-doped TiO2-modified carbon-supported Pt (Pt/Ti0.9Sn0.1O2–C) as an electrocatalyst for a DMFC system. The synthesized Pt/Ti0.9Sn0.1O2–C electrocatalyst revealed high catalytic activity and CO tolerance toward MOR. The enhanced catalyst activity was due to the high content of OH groups on the Ti0.9Sn0.1O2 electrocatalyst sample and the strengthened metals and support interactions. In addition, Lv et al. [122] also reported in their work that the addition of TiO2 could not only facilitate CO removal and hinder CO formation on Pt surface during methanol oxidation, but it can also prevent the agglomeration and corrosion of Pt, which can be concluded from strong metal-supports interaction between TiO2–C and Pt.黄等人。 [123] revealed that a TiO2-coated carbon nanotube support for Pt electrocatalysts could be prepared via a one-step synthesis. Hao et al. [124] developed a new catalyst composed of Pt nanoparticles deposited on graphene with MoO3. These catalysts exhibited high catalytic activity toward MOR and high resistance to CO species. However, the size of MoO3 must be tuned by controlling the metal oxide loading.
The selection of metal oxide such as MnO, RuO, CeO, SnO2, MgO, and V2O5 as additional component in electrocatalyst of Pt because of their low cost, good electrochemical properties, and have proton-electron intercalation properties [125]. From the catalytic activity aspect, it can be summarized that the addition of these metal oxides can enhance the electrocatalytic activity of DMFC and other fuel cells. The incorporation of these conducting metal oxides together with Pt catalyst could also facilitate the oxidation process of CO intermediate molecules. Hence, these types of metal have high potential to be used together with platinum as anode electrode.
Carbon support
To improve the utilization of the Pt catalysts, the carbon support is also another useful approach to be used together with Pt. Carbon materials are largely used as catalyst support because of its special properties such as relatively stable in both acid and basic electrolyte, good conductivity, and provide high surface area for dispersion of metal catalyst. It is believed that carbon materials have a strong effect that can influence the electrocatalysts properties such as metal particle size, morphology, metal dispersion, alloyed degree, and stability. Carbon supports can also affect the performance of supported catalysts in fuel cells, such as mass transport and catalyst layer electronic conductivity, electrochemical active area, and metal nanoparticle stability during the operation.
Currently, a great concern of the development in the nanotechnology field, especially carbon nanomaterials synthesis, is to create more stable and active supported catalysts. Support materials of nanoparticles are believed to be the most promising materials for catalytic activity in fuel cells, including the DMFC system. Pt has been traditionally used as nobel catalysts for many fuel cells application [126,127,128]. However, the high cost and low reserve are hindering commercialization of fuel cells and driving researchers to make the utmost of the catalyst. According to this problem, the major effort has been done toward nanoscaling of the catalyst nanoparticles to form more active sites per mass unit. The morphology, structure, and activity of the catalyst, and correspondingly the whole lifetime of a cell, thus strongly depend on the catalyst support [129]. Table 2 shows the preparation, physical properties, performance, and activity of Pt-based supported carbon done by groups of researchers. The details of Pt-based supported carbon will be performed in the following sections:“Graphene Support” to “Carbon Nanocoils”.
图>Graphene support
Graphene has many extraordinary properties; it exists as a two-dimensional carbon (2-D) form, which is called a crystalline allotrope, one-atom-thick planar flat sheet of sp2 tightly bonded carbon atoms with a thickness of 0.34 nm. Its carbon atoms are packed in a regular atomic-scale chicken wire (hexagonal) pattern [92, 119]. The theoretical specific surface area of graphene is 2630 m 2 g −1 , which is much larger than that of carbon black (typically less than 900 m 2 g −1 ) and carbon nanotubes (100 to 1000 m 2 g −1 ) and similar to that of activated carbon [130]. Graphene has high potential as a metal support [131, 132, 133] [33] due to its high surface area [134] for better catalyst/metal dispersion [135], high electrical conductivity [136], and good thermal properties [137, 138]. Moreover, the functionality of graphene support can be modified by changing it surface structure, and hence contribute to its potential applications, such as in fuel cells, energy storage, electrochemistry, supercapacitors, and batteries [138,139,140,141,142]. Figure 4 illustrates the preparation steps to obtain the graphene nanosheets (GNS), while Fig. 5 shows their TEM images [143]. It can be clearly observed that the thickness of the GO with many typical wrinkles obviously decreases compared to graphite. This can be explained by the presence of the rich oxygen-containing functional groups over the surface of GO [132]. Besides, both resulting GN-900 and GN-900-C contained of a large size of nanosheets structure, but the GN-900-C comprised more transparent than the GN-900.
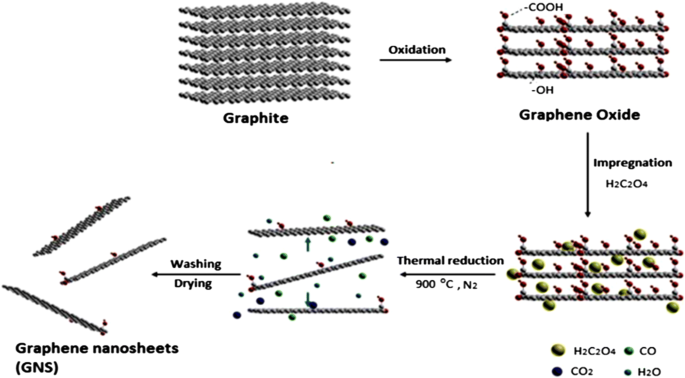
illustration of the preparation of graphite oxide to graphene nanosheets (GNS) by using oxalic acid [143]
图>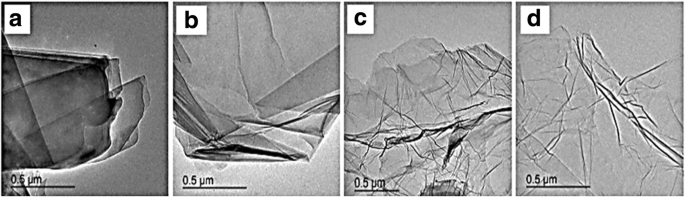
TEM images of graphite (a ), GO (b ), GN-900 (c ), and GN-900-C [143]
图>The discovery of graphene sheets began around 2000 by mechanical extracting process from 3D graphite source [133]. Graphene can be obtained by several synthesis methods such as hydrothermal [144], chemical reduction [143], chemical vapor deposition, and electrochemical. Ma et al. [145] enhanced the electrocatalytic activity of Pt nanoparticles by supporting the Pt nanoparticles on functionalized graphene for DMFC. Functionalized graphene was prepared by methyl viologen (MV) and Pt/MV–rGO electrocatalyst was synthesized by a facile wet chemical method. They also reported that the higher catalytic activity of Pt/MV–RGO was attributed to the synergetic effect between MV and rGO.
Meanwhile, Zhang et al. [146] modified the graphene support with graphene nanosheets through Hummer’s method, followed by polymerization of aniline (as nitrogen source). The TEM images for Pt/NCL-RGO and Pt/RGO electrocatalysts show that the aggregation between separated graphene sheets was decreased by nitrogen-doped carbon layer (NCL), leading to a better dispersion of the Pt catalyst on the graphene nanosheets support and better electroactivity and stability toward methanol electrooxidation (MOR). Presence of NCL successfully prevented the aggregation of graphene nanosheets as the Pt nanoparticles supporting material.
In 2011, Qiu et al. [135] successfully synthesized nanometer-sized Pt catalyst via sodium borohydride reduction method with an average particle size of only 4.6 nm. These Pt nanoparticles showed an even dispersion of Pt catalyst on graphene oxide support and very high electrocatalytic activity toward MOR by controlling the percent deposition of Pt loaded on the graphene. In another study conducted by Ojani et al. [147], for synthesized Pt-Co/graphene electrocatalyst, it was shown that graphene nanosheets improved the electrocatalytic behavior and long-term stability of the electrode. In addition, the Pt-Co/G/GC electrocatalyst showed great stability toward MOR. The catalytic performance toward MOR can also be improved by using cobalt core–platinum shell nanoparticles supported on surface functionalized graphene [148]. This enhanced catalytic activity could be attributed to the poly (diallyldimethylammonium chloride) (PDDA) that plays a crucial role for dispersion and stabilization of Co@Pt catalyst on graphene support. PDDA-functionalized graphene provided the higher electrochemical active surface area [149, 150].黄等人。 [138] also studied a PtCo-graphene electrocatalyst with outstanding catalytic performance and high CO tolerance toward the MOR, which far outperformed Pt-graphene and PtCo-MWCNT electrocatalysts with the same ratio of Pt and carbon content. Figure 4 shows the formation of a graphene-PtCo catalyst prepared from a graphite source. Sharma et al. [57] synthesized Pt/reduced graphene oxide (Pt/RGO) electrocatalyst using a microwave-assisted polyol process, which sped up the reduction of GO and formation of Pt nanocrystals. They compared Pt/RGO to a commercial carbon support (Pt/C), which exhibited high CO tolerance, high electrochemically active surface area, and high electrocatalytic activity for the MOR. In a previous study, Zhao et al. [139] reported that the unique 3D-structured Pt/C/graphene aerogel (Pt/C/GA) exhibited greater stability toward MOR with no decrease in electrocatalytic activity. Moreover, the Pt/C/graphene aerogel also exhibited significantly higher stability to scavenge crossover methanol at high potential in an acidic solution compared with the commercial Pt/C electrocatalyst. At the initial catalytic stage, the Pt/C electrocatalyst lost approximately 40% after 1000 CV cycles. In contrast, the Pt/C/graphene aerogel only lost 16% of the initial catalytic activity. After 200 cycles of CV, the current density of Pt/C/graphene aerogel was much higher with a remarkably higher stability than that of Pt/C electrocatalyst. Meanwhile, Yan et al. [151] demonstrated highly active mesoporous graphene-like nanobowls supported Pt catalyst with high surface area of 1091 m 2 g −1 , high pore volume of 2.7 cm 3 g −1 , and average pore diameter of 9.8 nm obtained by applying a template synthesis method. In addition, the Pt/graphene bowls also achieved high performance toward MOR with a current density value of 2075 mA mgPt −1 , which was 2.87 times higher than that of commercial Pt/C (723 mA mgPt −1 )。 The onset potential for the Pt/graphene bowls toward methanol electrooxidation was negatively shifted by approximately 160 mV compared with that to the latter and showed CO resistance. Figure 6 shows the proposed schematic for the formation of PtCo catalyst on reduced-GO (rGO) support [51]. It is described that the formation of graphene oxide nanosheets from oxidation of graphite powder leads to the increase in interlayer “d” spacing of stacked graphitic sheets from 0.34 to 0.78 nm due to the presence of various oxygen-containing functional groups. The oxygen-containing functional groups act as anchor sites for the well-dispersed Pt and PtCo nanoparticles on rGO sheets, and used for efficient electrooxidation of methanol.
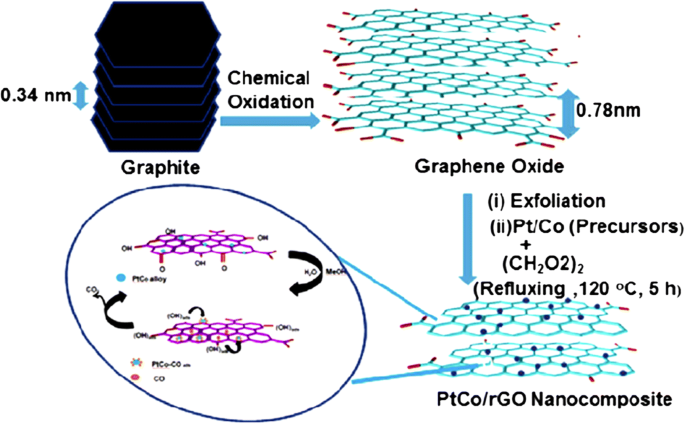
Illustrates the schematic formation of graphene supported Pt-Co catalyst [51]
图>We can conclude that the reduce graphene oxide (rGO), graphene, modified graphene as supporting material exhibited high electrocatalytic activity toward methanol electrooxidation process. A lot of studies have been reported related to the particle size distribution and size, morphologies, and catalytic activities of Pt and Pt alloys using graphene as supporting material, which showed great improvement in fuel cell performance as mentioned and discussed above. Thus, graphene support can be further studied for better fuel cell performance.
Multiwall Carbon Nanotube and Single-Wall Carbon Nanotube Support
Several years ago, Jha et al. [140] prepared multiwall carbon nanotube (MWCNTs) via chemical vapor deposition using an AB3 alloy hydride catalyst. Platinum-supported MWCNT (Pt/MWCNT) and platinum-ruthenium-supported MWCNT (Pt-Ru/MWCNT) electrocatalysts were prepared by chemical reduction. The performance of these electrodes was studied at different temperatures, and the results demonstrated a very high power density of 39.3 mW cm −2 at a current density of 130 mA cm −2 , which could be attributed to the dispersion and accessibility of the MWCNT support and Pt-Ru in the electrocatalyst mixture for the methanol oxidation reaction. This was also done by other researchers that using different catalyst supported MWCNT for DMFC system [152,153,154,155]. Meanwhile, Wu and Xu [156] compared MWCNT-supported Pt and single-wall carbon nanotube (SWCNT)-supported Pt. Figure 7 shows that the TEM images of Pt catalyst was deposited on MWNT and SWNT electrodes through the electrodeposition technique. The Pt particles in Pt-SWNT (Fig. 7b) looked closer contact with the network of entangled and branched bundles of SWNT support, and the shape is closer to highly exposed sphere. The benefits of the SWCNT support are due to its greater electrochemical surface-active area and easier charge transfer at the electrode/electrolyte interface because of the graphitic crystallinity structure, rich amount of oxygen-containing surface functional groups, and highly mesoporous and unique 3D-structure of SWNT. The electrodeposition technique carried out by them contributed to higher utilization and more uniform dispersion of Pt particles on its support.

TEM images for the Pt on MWCNT(a ) and SWCNT (b ) [156]
图>Then, Wang et al. [157] reported the high performance of modified PtAu/MWCNT@TiO2 electrocatalyst prepared via deposition-UV-photoreduction for DMFC, which also exhibited high CO tolerance.赵等人。 [126] studied 3D flower-like platinum-ruthenium (PtRu) and platinum-ruthenium-nickel (PtRuNi) alloy nanoparticle clusters on MWCNTs prepared via a three-step process, and the best ratios obtained from their experiments for the PtRu and PtRuNi alloys were 8:2 and 8:1:1, respectively. Another group, i.e., Zhao et al. [158], found a higher current density toward MOR and better activity for MWCNT-supported PtWC compared with Pt/C electrocatalyst. These results were attributed to the factors of the synergistic effect between the Pt catalyst and the WC component, high CO tolerance from the bifunctional effect of the Pt catalyst and the WC component, and strong interaction between metals and WC in the electrocatalyst composite.
As a summary, both of MWCNT and SWNT support in terms of structural, surface, and electrochemical properties have their own characteristics as supporting material that remarkably enhanced their performance in catalysis of methanol oxidation process. However, as a comparison, SWCNT possess a high degree of graphitization, highly mesoporous 3D structure, and contain more oxygen-containing functional groups at its surface sites. In relation with these properties, the SWCNT exhibits a higher electrochemically accessible surface area and faster charge transfer rate at the electrode/electrolyte interface.
Carbon Nanotube Support
文等人。 [144] proposed that carbon nanotubes (CNTs) support could improve fuel cell performance; for example, Pt can be fixed to the inner wall and the outer wall of CNTs and may cause improvement in the electrocatalytic properties of platinum-CNTs. Yoshitake et al. [159] proposed that fuel cells using CNTs as the catalyst support produced larger current densities. The addition of binary or other components to the electrocatalysts for methanol electrooxidation overcomes the problems related to catalyst poisoning caused by CO during the reaction. Therefore, new electrocatalyst carbon supports, such as carbon nanotubes [160, 161], are being actively developed to significantly improve fuel cell performance. Kakati et al. [128] successfully synthesis the PtRu on CNT/SnO2 for anode catalyst DMFC via hydrothermal process. It has been found that the presence of SnO2 provide a high durability property for the catalyst and the presence of SnO2 in the district of Pt could supply oxygen-containing functional groups for the removal of CO intermediate molecules from the Pt surface sites during electrooxidation of methanol. Generally, the decomposition methanol occurs at Pt surface sites; meanwhile, the decomposition of water occurs at SnO2 surface sites to form oxygen-containing species which then react with CO intermediate molecules. However, as support material, the conductivity property of SnO2 still needs to be enhanced. Kakati et al. [128] also proposed the schematic diagram of the formation of PtRu on CNT/SnO2 composite as shows in Fig. 8, and FESEM images of CNT/SnO2 composite support (a and b) and PtRu/SnO2/CNT composite electrocatalyst (c and d) in Fig. 9.
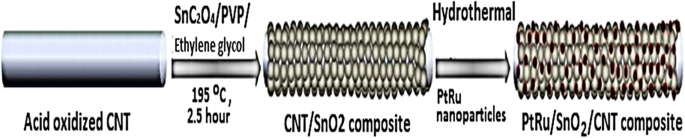
Illustrates the schematic diagram for the formation of PtRu/SnO2/CNT composite [128]
图>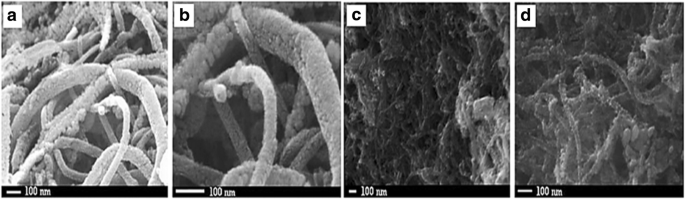
FESEM images of CNT/SnO2 composite support (a , b ) and PtRu/SnO2/CNT composite electrocatalyst (c , d )
图>Chien et al. [127] proposed that the high catalytic performance of Pt-Ru/CNT for MOR can be attributed to the presence of CNT as the carbon support material with several factors:(i) the as-synthesized Pt-Ru/CNT electrocatalyst owns the ideal nanosized particles and composition to increase catalytic activity, (ii) the presence of functional group on the CNT surface results in high hydrophilicity of CNT, which produces better electrochemical reaction on the electrode area, and (iii) the high electronic conductivity of the CNT support lowers the resistance in MOR. Jeng et al. [150] prepared Pt-Ru/CNT electrocatalyst via a modified polyol with a PtRu composition ratio of 1:1, exhibiting high catalytic activity toward MOR and better performance than that of commercial PtRu/C. Show et al. [162] reported that Pt catalyst with a size of less than 10 nm can be obtained by dispersing the Pt particles on a CNT surface using the in-liquid plasma method, and excellent performance was demonstrated by the electrical power achieving 108 mW cm −2 [162]. The in-liquid plasma method was also used by Matsuda et al. [163] that can applied to obtain nanometer-sized Pt catalyst on support material that remarkably enhanced the fuel cell performance.
To be concluded, high electric conductivity, large surface area, excellent chemical and electrochemical stabilities, quasi one-dimensional structure, and good morphology as the supporting materials are the key factors of carbon nanotubes (CNTs) in enhancing the DMFC performance. In addition, carbon support materials such as CNTs which contribute a large effect on metal distribution and size have also been proven to be an essential to the electrocatalysts to achieve high catalytic activity during methanol oxidation process.
Carbon Nanofiber Support
Steigerwalt et al. [164] reported the successful synthesis of PtRu alloy that was widely dispersed on a graphene carbon nanofiber (CNF) support as an electrocatalyst in DMFC. The catalytic activity was enhanced by ~ 50% relative to that recorded for an unsupported PtRu colloid anode electrocatalyst. Meanwhile, Wang et al. [152] reported that Pt/CNF nanocomposites obtained by the reduction of hexachloroplatinic acid (H2PtCl6) precursor with formic acid (HCOOH) in aqueous solution containing electrospun CNFs at room temperature showed a higher current density than other prepared Pt/CNFs and was approximately 3.5 times greater than that of the E-TEK Pt/C electrocatalyst. Another research carried out by Giorgi et al. [153] described a CNF and bimetallic PtAu electrode with a single layer and both diffusive and catalytic functions using a decreased noble metal amount (approximately five times less) with a consequent large cost reduction. In addition, the bifunctional electrocatalytic properties were also active for the MOR on the PtAu nanoparticle catalysts [154]. Calderón et al. [155] reported PtRu/CNF prepared via reduction using sodium borohydride (NaBH4), methanol, and formate ions. This electrocatalyst synthesized by SFM was heat-treated (denoted as SFM TT), which improved its electrocatalytic activity during MOR. Later, Maiyalagan [165] reported that the addition of silicotungstic acid acted as a stabilizer for the PtRu particles on CNT support. The PtRu-supported CNT was prepared by microwave heating of an ethylene glycol (EG) solution of STA, H2PtCl6.6H2O (as Pt precursor), and RuCl3.xH2O (as Ru precursor) with CNF suspended in the solution. The Pt and Ru precursors were loaded on CNF by conventional impregnation method. The results revealed that the PtRu nanoparticles are uniformly dispersed on carbon nanofiber support, with an average particle size of 3.9 nm enhanced the catalytic activity toward methanol electrooxidation. As a conclusion, the carbon nanotubes supporting material with high electronic conductivity and high surface area gives an advantage of better dispersion for the Pt or Pt alloys deposition. The higher the surface area of supporting material can reduce the agglomeration of metal particles on it, thus can produce better catalyst morphology for better fuel cell performance.
Mesoporous Carbon Support
Mesoporous carbon (MPC) support is another ideal candidate as an electrocatalyst support material in DMFC and fuel cell. Generally, mesoporous carbons are divided into two classes based on their structures which are ordered mesoporous carbons (OMCs), with highly ordered pore structure and uniform pore size, nonordered mesoporous carbons with irregular pores. Other than that, OPC can be produced by using high quality of SBA-15 silica and sucrose as carbon source template. To prepare the high quality of SBA-15 SBA-15 sample, triblock copolymer, EO20-PO70EO20 (Pluronic P123, BASF), as the surfactant and tetraethyl orthosilicate (TEOS, 98%, Acros) as the silica source are used, as reported by literature [166,167,168]. The synthesis of MPC starts from synthesis of SBA-15, followed by calcination process.
A well-dispersed and ultralow Pt catalyst (PtFe) supported on ordered mesoporous carbon (OMC) was prepared via a simple route and showed superior catalytic activity. The PtFe alloy with a size range of 3–5 nm was homogeneously dispersed on the CMS with a very high specific surface area of more than 1000 m 2 g −1 [169]. The incorporation of Fe was discussed in the previous section (“Performance of Various Types of Pt-Based Catalysts” section and “Performance of Pt-Based Alloys” section). The high specific surface area of mesoporous carbon support can be produced by carbonization process of a resorcinol-formaldehyde polymer with a cationic polyelectrolyte as a soft template [160]. The performance of Pt/MPC also related to the synthesis/preparation method as done by Kuppan and Selvam. Kuppan and Selvam [167] synthesized four type of Pt/mesoporous carbon by using different reducing agent which are NaBH4, EG, hydrogen, and paraformaldehyde. From there, the Pt/mesoporous carbon synthesized using paraformaldehyde as reducing agent for showed highest current density. The highest in catalytic was attributed to the use of paraformaldehyde that gives the smallest Pt particle size (4.5 nm), and the highest ECSA (84 m 2 /g) belongs to Pt/mesoporous carbon.
Wang et al. [161] synthesized a Pt@WC/OMC electrocatalyst composite, in which the composite was platinized using a pulsed microwave-assisted polyol technique. The OMC produced in this synthesis exhibited high surface area property. The Pt@WC/OMC electrocatalyst also showed high activity, desirable stability, and CO tolerance toward MOR. In another work done by Zhang et al. [170], the ordered CMS had a unique hierarchical nanostructure (with a 3-D structure) with ordered large mesopores and macropores that facilitated the dispersion of Pt nanoparticles and rapid mass transport during the reactions.
To maximize the use of Pt particles, the support materials should have uniform dispersion, high utilization efficiency, and desirable activity and stability. Moreover, the good supporting materials must be suitable for surface chemistry, high loading of Pt dispersion, and some functional roles. Additionally, based on the previous studies as discussed above, the ordered mesoporous carbons with large pore sizes are highly desirable for fast mass transfer and, thus, enhance the catalytic activity especially in the reaction involve large reactants molecules.
Carbon Black
Carbon black (CB) is one of the commercial carbon support that has been used till now. There are many types of CB such as Vulcan XC-72, Black Pearl 2000, Denka Black, Shawinigan Black, Ketjen EC-300J, etc. [171, 172]. CB is commonly used as a carbon support material for electrocatalysts because it possesses high porosity properties, which make it suitable as a potential support material for the catalyst layer in PEMFCs and DMFCs as reported in provided literatures [173,174,175,176,177,178,179,180]. The comparison of the several carbon black support was reported by Wang et al. [181] who investigated the effect on DMFC performance using several types of carbon black such as Vulcan XC-72R, Ketjen Black EC 300J, and Black Pearls 2000 carbon black as additives/support for the Pt cathode catalyst. From the experiments, the results showed that Ketjen Black EC 300J was the most useful carbon support for increasing the electrochemical surface area and DMFC performance of the cathode catalyst.
Nowadays, CB is commercial carbon support for many fuel cell systems. Generally, it is used for the comparison with new or modified catalyst [125]. The following Table 3 summarizes the commercial carbon black and its properties for fuel cell application. There are so many modifications among carbon support materials and development of new carbon support for enhance fuel cell performance; however, commercial carbon black still is used in many fuel cell applications especially for the comparison with new or modified catalyst.
图>Carbon Nanocoils
Celorrio et al. [182] proposed carbon nanocoils (CNCs) as a PtRu support in their experiment, indicating that the electrocatalyst performance was strongly dependent on the synthesis method. CNC-supported electrocatalysts showed better electrochemical behavior than E-TEK electrocatalysts, and better electrocatalytic behaviors toward CO and methanol oxidation were achieved using CNC as a support material [182]. Sevilla et al. obtained highly graphitic CNCs from the catalytic graphitization of carbon spherules via the hydrothermal treatment of different saccharides which are sucrose, glucose, and starch [183]. They demonstrated that the high electrocatalytic activity of the CNCs is due to the combination of good electrical conductivity of their graphitic structure and high porosity property, which allows much less diffusional resistance of reactants/products. Two years later, Sevilla et al. [184] reported highly dispersed Pt nanoparticles on graphitic CNCs with diameters in the range of 3.0–3.3 nm and a very fine particle size distribution. The electrocatalyst possessed large active Pt surface area (up to 85 m 2 g −1 Pt), high catalytic activity toward MOR (up to 201 A g −1 Pt), and high resistance against oxidation, which was noticeably greater than that of the Pt/Vulcan electrocatalyst. Celorrio et al. [185] obtained Pt/CNC electrocatalysts via the impregnation method, which showed that a combination of Pt and CNCs facilitated the CO oxidation process.
Conductive Polymer Supports
Choi et al. [186] synthesized PtRu alloy nanoparticles with two types of conducting polymers, i.e., poly(N -vinyl carbazole) and poly(9-(4-vinyl-phenyl)carbazole), as the anode electrodes. Electrochemical and DMFC tests showed that these nanocomposite electrocatalysts were beneficial in a DMFC system, but their catalytic performance was still lower than that of a carbon supported electrode. Thus, they suggested that higher electrical conductivity of the polymer and lower catalyst loss are required in nanocomposite electrodes to achieve better performance in a DMFC. Choi et al. [171] and Kim et al. [172] prepared polyaniline (PANi) as a support material for PtRu catalyst in a DMFC system. PANi is a group of conductive polymers with high electronic conductivity and a methanol oxidation current similar to that of carbon-supported PtRu catalyst. Then, Kim et al. [172] conducted catalytic tests to compare PtRu/PANi support with PtRu/carbon support, showing that the enhanced catalytic activity of PtRu/PANi was due to (i) the high electrical conductivity of the polyaniline support, (ii) the increase of electrochemical surface area of the prepared electrocatalyst, and (iii) the higher ion diffusion behavior. In another study, Amani et al. [74] synthesized PtSn supported by C-PANI as an electrocatalyst with different Pt:Sn atomic ratios using the impregnation method. The PtSn/C-PANI electrocatalyst with a ratio of 30:70 showed outstanding performance in the methanol electrooxidation, and the current density was approximately 40% higher than PtRu/C and 50% higher than Pt/C-PANi. The CO tolerance and stability were improved compared to that of PtRu/C, and the methanol crossover was reduced. Yaldagard et al. [173] studied the electrocatalytic performance of Pt/PANi/WC/C electrocatalyst for methanol electrooxidation (MOR) and oxygen electro-reduction (ORR), and it exhibited higher MOR activity, high CO resistance, and improved stability compared to Pt/C electrocatalyst in the presence of methanol.
吴等人。 [174] presented polypyrrole nanowire networks (PPNNs) as the anodic microporous layers (MPLs) of passive DMFC. In passive DMFC system, the novel MPL achieved a 28.3% increase in the power density from 33.9 to 43.5 mW cm −2 compared with the conventional layer with a similar PtRu (1:1). The high performance was due to the presence of PPNNs, which expressively improved the catalyst utilization and mass transfer of methanol on the anode. Besides, Selvaraj and Alagar [175] prepared Pt-Ru nanoparticle-decorated polypyrrole/multiwalled carbon nanotubes (Ppy/CNT) via the in situ polymerization of Ppy on CNTs containing ammonium peroxydisulphate (NH4)S2O8 as an oxidizing agent at the temperature range of 0–5 °C, followed by deposition of Pt particles on PPy-CNT composite films via chemical reduction to produce Pt/PPy-CNT. It was found that the PtRu particles deposited on PPy–CNT composite films exhibited higher catalytic activity and stability toward MOR compared to Pt/PPy-CNT. So far, the investigation on polymer as supporting materials is not much as carbon support materials. From aspect as supporting materials, the performance of polymer support was not good/excellent as carbon support. Further studies are needed in the future for better electrocatalytic activity and DMFC performance.
Problems and Limitations of Using Pt for DMFC Systems
There are two major challenges in the development of new DMFC catalysts:(i) performance, including the catalytic activity, reliability, and durability; and (ii) catalyst cost reduction. Two major problems arise in DMFC when using pure Pt alone as the anode catalysts:(1) slower kinetics oxidation of methanol, even on some state-of-the-art anode catalysts, and methanol crossover through the membrane, which not only lowers cathode performance but also reduces fuel efficiency. To develop successful fuel cell technology, including DMFC technology, new catalysts must be investigated to improve the performance and reduce the cost. Reduction of the catalyst cost remains a major challenge. Currently, platinum is one of the most effective electrocatalysts for DMFC due to its high catalytic activity for methanol oxidation, but because it is a precious metal, platinum usage is challenging and limited [176, 177]. Therefore, many scientists have attempted to find materials that can behave like Pt catalysts. One problem with the MOR in DMFCs is that CO is produced as an intermediate reaction product when using Pt catalyst and has strong binding energy on platinum particles, poisoning the active sites of the platinum surface area [58]. Therefore, CO must be removed by oxidizing it from the Pt surface using another material with high resistance to CO poisoning. For example, Hwu et al. proposed Pt-modified WC catalyst that has remarkable resistance to CO poisoning [178]. On the other hand, they also suggested that CO tolerance originates from the lower CO desorption temperature on pure and Pt-modified WC compared to pure Pt.
There are many solutions that can be applied to reduce the cost of Pt, overcome or minimize the formation of CO species during methanol oxidation, and increase the kinetics of methanol oxidation, such as alloying with other metals or transition metals, the incorporation of metals, metal nitrides, and metal oxides and the use of carbon supports as discussed in this paper. However, to overcome this problem, we need to understand the formation of CO on Pt sites particle, and understanding of the mechanism of the anode reaction in DMFCs. Unfortunately, it has limited amount of mechanistic insight to be studied, because this reactions involve complex mechanism path with many possible intermediate molecules and also competing reaction pathways [179]. For Pt catalytic mechanism, it has been suggested by a direct reaction path. Unfortunately, the use of Pt on other metals has limited mechanistic information available. Figure 10 represents the reaction path for methanol electrooxidation and their possible intermediates molecules formed during the process. Black arrows show direct path, while green arrows show the indirect mechanism for CO2 formation as a final product. In the direct mechanism, the reaction path does not involve a CO intermediate, and CO2 is formed directly from methanol. In contrast, indirect mechanism forming a CO intermediate molecule and subsequently it is oxidized to CO2 product. Notably, CO is the most stable molecule of all the intermediates on Pt during MOR. The stability of CO causes it to be a main reason for the extensive CO poisoning problem that is often found on Pt catalyst.
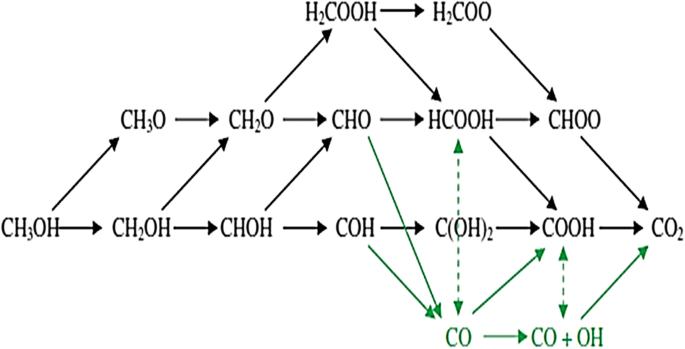
Schematic of the reaction paths and possible intermediates molecules considered in methanol electrooxidation [237]
图>First step in the mechanism of methanol decomposition reaction on Pt is the activation of methanol molecule. It can take place via hydrogen abstraction from either the carbon or the oxygen atoms. Further step, hydrogen abstraction creates formaldehyde (CH2O) or hydroxymethylene (CHOH), followed by formyl (CHO) or COH. In the direct mechanism, instead of stripping off the final hydrogen from CHO or COH molecule to CO, a water molecule will release a proton/electron pair and resulting to OH species that can further bind with the carbonaceous species to form dihydroxycarbene (C(OH)2) or formic acid (HCOOH). This step is called hydroxyl addition process. The next step is followed by dehydrogenation to form either formate (HCOO) or carboxyl (COOH) molecule, with subsequent dehydrogenation to form CO2 as the final product of reaction. In addition, an alternative direct mechanism involve the stripping of a proton/electron pair from water and addition of the resulting hydroxyl to CH2O, subsequently to H2COOH, which then undergoes dehydrogenation to form HCOOH or dioxymethylene (HsCOO). The HsCOO molecule can then undergoes dehydrogenation to HCOO and finally to CO2. Besides, in the indirect mechanism, CHO or COH species are directly dehydrogenated to CO. Water is dissociated separately on the surface to form OH, and the two surface species react together to form CO2 gas in a way similar to the water-gas-shift reaction [187]. This indirect mechanism occurs because less energy is required to form CO than CO2. Strong adsorbed CO intermediate form on the Pt surface sites revealed a major problem at the anode site of DMFC. Formation of this intermediate species can cause deactivation Pt catalyst. Furthermore, the rate of kinetic methanol oxidation for DMFC is slower. Therefore, to increase the resistance of Pt catalyst to CO poisoning on the electrodes, Pt alloy or hybrids, such as PtRu, PtSn, PtMO, PtPb, PtFe, PtCo, PtNi, PtRuOs, PtRuMo, PtRuSn, PtRuNi, etc. (as mentioned and discussed in “Performance of various types of Pt-based catalysts” section), are usually employed as electrocatalyst materials on DMFC anodes. Addition/incorporation of these alloys to Pt can prevent the adoption of CO on Pt surface by decreasing the oxidation overpotential of the anode [84].
Conclusion and Prospects
Great progress has been made in recent years in the development and optimization of new catalysts using Pt-based catalysts and carbon and conductive polymer supports for DMFC anode catalyst. Some new carbon materials, such as nano- or mesostructured carbons, have been demonstrated as highly potential catalyst support materials, although their applications face challenges in terms of synthesis, metal loading, and electrode preparation. The combination of platinum as the best metal catalyst for DMFC and an excellent carbon support could produce breakthroughs in the investigation of a new DMFC anode catalyst in the future. Since platinum is an expensive metal, it is necessary to reduce the amount of Pt used in the electrocatalyst. Therefore, this paper presented more than 100 studies on the electrocatalytic activity and performance related to Pt-based electrocatalysts and various carbon and conductive polymer supports. The main problems related to the platinum electrocatalyst, such as carbon monoxide formation during the methanol oxidation reaction and the poor kinetics of methanol oxidation, could be overcome using additional materials and various supports, as reported in the research presented in this paper.
Many studies conducted in the recent years to reduce the loading amount of Pt catalyst and to increase the percentage utilization efficiency, and hence, enhance the electrocatalytic activity of Pt toward the oxygen reduction reaction (ORR) and methanol electrooxidation reaction (MOR), were discussed in this paper. Pt has been alloyed with many transition metals such as Fe, Co, Ni, Ir, Ru, Rh, and Pd, resulting in higher catalytic activity for the DMFC system. The incorporation of these materials also resulted in good dispersion on the carbon and polymer supports, which showed higher performance in the DMFC test compared to the use of Pt metal alone. Various carbon support sources, namely activated carbon (AC), carbon black (CB), multiwall carbon nanotubes (MWCNTs), carbon nanofibers (CNFs), carbon nanotubes (CNTs), graphene, and conductive polymer supports, have been used with Pt-based catalysts to improve their catalytic performance. Additionally, Pt-based alloy catalysts have been designed as hollow mesoporous PtNi, nanowire PtRu, and nanodendritic PtRh, which showed improved electrocatalytic activity and superior electrocatalytic performance. Meanwhile, 3-D Pt/C/graphene aerogel demonstrated enhanced stability toward methanol electrooxidation. The work performed by researchers showed that the electrocatalytic activities of nanoparticles Pt alloy catalysts depend on several factors such as the synthesis method, condition of experiments (such as temperature and pH), alloy composition/ratio, precursors, and thermal treatment. For the future study, it should be extended to the optimization of the geometry and structure of previous studies that revealed active Pt alloys can increase their electrocatalytic activity and stability and the application of support materials for fuel cell applications. For example, current research that have been done by Liu et al. 2017 [188] shows the excellent performance of platinum. From theoretical calculations, it revealed that the main effective sites on platinum single atom electrocatalysts are single-pyridinic-nitrogen-atom-anchored single-platinum-atom centers, which ascribed to the tolerant CO in MOR. They also suggested that carbon black supported used together with Pt single atom is effective in cost, efficient, and durable electrocatalyst for fuel cell application. According to the above study, herein, we can conclude that the modification on structure and morphology of precious metal such as platinum could also remarkably increase the performance of electrocatalyst, but in the same time can reduce the overall cost of fuel cell for commercialization.
To improve the morphologies of Pt and Pt alloys, carbon support material also need further study. Nanoporous metals become an interesting part of catalyst to be studied for fuel cell application. It is determined very suitable for fuel cell catalysts because they possess high surface area, three-dimensional (3D) network structures with adjustable ligament/pore sizes suitable for mass transport, and electron conduction. Around 2017, Li et al. successfully carried out modification on Pt-Pd-Au trimetallic surface as cathode for oxygen reduction reaction [189]. The surface evolution of 3-D Pt-Pd-Au trimetallic greatly enhanced the ORR activity and highly stable as ORR catalyst. The modification of PtNi alloy also done by Li et al. 2016 [190] showed ultrafine jagged platinum nanowire with highly large ECSA that exhibits enhanced mass activity of ~ 50 times higher than state-of-the-art commercial Pt/C catalyst, while Bu et al. 2016 [191] reported highly uniform PtPb/Pt core/shell nanoplate with biaxially strain extremely active, stable for anodic oxidation reactions, and great performance compared to commercial Pt/C in both methanol oxidation reaction (MOR) and ethanol oxidation reaction (EOR). Since the nanostructured platinum becomes an efficient catalyst for fuel cells as well as various industrial chemical reactions. Thus, these modifications on surface of Pt particles electrocatalysts could also to be applied in MOR for future DMFC.
On the other hand, to reduce the consumption of the Pt catalysts, the modification of the carbon support is also another useful way. This not only improves the transport capacity of protons but also reduces the usage of Nafion, which can cut the cost of the fuel cell. Moreover, with regards to the carbon support for the ORR catalysis, the hydrophobic carbon support material is required to allow water (product) to be quickly removed from the catalyst surface sites, and oxygen (reactant) to access the active sites. In contrast, the MOR catalysis requires a certain degree of hydrophilic carbon support. It can be achieved by the modification of the carbon support materials. By combination of modified carbon support materials and development of new carbon support with Pt metal catalyst, it is possible to get an ideal electrocatalysts for direct methanol fuel cell technology. Combination of Pt metal with varied carbon supports with different specific surface areas, structures, pore sizes, electronic properties, and morphologies could be great catalyst to be studied for future DMFC.
Carbon support also influence the overall performance for DMFC. Vulcan XC-72R, which is a commercial carbon support, has a large surface area, appropriate particle size, and good electrical conductivity for good support. However, in the process of depositing metal particle on these support with loading of 40% or more, the particle size of metal increased quickly, which is a disadvantage for DMFC, because a higher metal loading is used to give a better performance. In addition, multiwalled carbon nanotubes (MWCNTs) and carbon nanofibers (CNFs) with relatively smaller surface area, large diameter, and high aspect ratio could be very difficult to deposit a catalyst with high loading metal (40% and more). Therefore, modification of MWCNTs and CNFs support must be done to improve its surface area, surface functional groups, and reduce the wall thickness to achieve outstanding performance for direct methanol fuel cell even though high loading metal catalyst is consumed. As well, a great and important part to be further studied in DMFC system is about the anode and cathode catalyst preparation approaches.
缩写
- CB:
-
Carbon black
- CH3O:
-
methoxy group
- CNC:
-
Carbon nano cage
- CNF:
-
Carbon nano fiber
- CNT:
-
Carbon nano tube
- Co:
-
Cobalt
- Co:
-
Cobalt
- CO:
-
Monoxide molecules
- CO2 :
-
Carbon dioxide
- DMFC:
-
Direct methanol fuel cell
- FC:
-
Fuel cell
- Fe:
-
Iron
- MOR:
-
Methanol oxidation reaction
- MPC:
-
Mesoporous carbon
- MWCNT:
-
Multi wall carbon nanotube
- Ni:
-
Nickel
- OMC:
-
Ordered mesoporous carbon
- ORR:
-
Oxygen reduction reaction
- PANi:
-
Polyaniline
- PEMFC:
-
Proton exchange membrane fuel cell
- Ppy:
-
Polypyrrole
- Pt:
-
Platinum
- Pt/MWCNT:
-
Platinum-supported MWCNT
- Pt-Ru/MWCNT:
-
Platinum-ruthenium-supported MWCNT
- Rh:
-
Rhodium
- Ru:
-
Ruthenium
- Sn:
-
Sternum
- SOFC:
-
Solid oxide fuel cell
- SWCNT:
-
Single-wall carbon nanotube
- TMN:
-
Transition metal nitride
纳米材料
- 用于改进诊断和治疗应用的多功能金纳米粒子:综述
- 用于合成和生物医学应用的荧光纳米材料的进展和挑战
- 用于超级电容器应用的石墨烯和聚合物复合材料:综述
- 通过静电纺丝法制备用于直接甲醇燃料电池的新型复合二氧化钛碳纳米纤维阳极催化剂的制备和表征
- 增强新型阳极 PdAu/VGCNF 催化剂在甘油燃料电池中的电氧化性能
- 石墨烯/WO3 和石墨烯/CeO x 结构作为超级电容器应用电极的评估
- 支持直接甲醇燃料电池的新型阳极催化剂:表征和单电池性能
- 金纳米团簇的生物医学应用:最新发展和未来展望
- 评论:用于油水分离的多孔金属过滤器和膜
- 荧光新糖蛋白金纳米团簇:合成及在植物凝集素传感和细胞成像中的应用
- 石墨氮化碳纳米基粒子的结构和性能(光催化)、制备技术及其应用的迷你评论
- 索尔维推出用于海上石油和天然气应用的高性能碳纤维胶带