Alcoa 追求卓越的可靠性
如果您受不了高温,最好不要在印第安纳州南部的 Alcoa Primary Metals 工厂求职。
喷火电解槽和填充熔融金属的坩埚可以将生产车间的环境温度推高至接近三位数。热量明显地从机器散发出来。汗水顺着工人的脸颊和背部流下。经常休息喝水和佳得乐是必要的。
这是一个对体力要求很高的环境,但第一段中提到的真正热量更多地与该特定工厂在铝冶炼行业中的地位有关。该工厂是美铝大型 Warrick 业务的一部分,建于 1950 年代后期,并于 1960 年代初开始为罐板行业生产原铝。
这是一个对年龄和技术敏感的行业中的老厂。 1980 年有 33 家美国冶炼厂在运营。今天有 13 家。今年全球铝产能的 6% 将在拥有 50 多年历史的冶炼厂生产。时钟在滴答作响。
对此状态,添加:
-
该工厂 25% 的员工目前有资格按年龄或服务年限退休;
-
工厂支付的工资在同行业中名列前茅;并且,
-
几年前,这家冶炼厂每吨铝的维护成本在全球美铝系统中排名第二。
你能感觉到热吗?这家工厂的每个员工都这样做。但是,维护和运营人员并没有等待似乎迫在眉睫的死亡,而是挺身而出并采取了行动。
“如果我们想维持这种生活水平并让这家工厂保持活力,我们就必须把它搞定,”美铝冶炼业务系统经理 Mark Keneipp 说。 “这是新的现实。你只需要处理它。”
从照镜子开始。
“尽管我们年事已高,但我们的挑战过去是,现在仍然是具有成本竞争力,”Keneipp 说。 “我们不再处于年龄曲线的前沿。我们必须有 15 到 20 年的时间来吸引美国铝业的资金。如果是 25 到 30 年,那就太好了。为此,我们必须不断证明自己是一家精益、具有成本竞争力、稳定且高效的工厂。”
这不是弱者的环境。但通过努力和坚持,会有丰厚的回报。
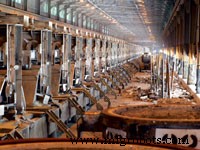
呼叫超时
维持 Alcoa Primary Metals 在印第安纳州南部制造业社区的业务始于公司层面。
1997 年,Alcoa 首席执行官 Alain Belda 开始将丰田生产系统 (TPS) 原则引入其公司的全球 250 个分支机构。
铝厂生产经理 Rodney Cunningham(左)、工艺协调员 Larry York 和高级工艺工程师布赖恩·奥迪 (Brian Audie) 站在美国铝业沃里克运营基地的一个空氧化铝罐内。该场地传统上使用四个这样的罐作为氧化铝的容器,氧化铝是铝冶炼过程中的关键成分。精益制造计划和批判性思维使工厂将规模缩小到两个储罐,为公司节省了大量资金。
TPS 是一种建立在“准时制”生产、消除浪费和快速解决问题基础上的精益制造理念。然而,印第安纳冶炼厂在实施该系统时有了一个重要发现。
“如果您的设备不稳定、不可预测,TPS、流量和精益就不起作用,”Keneipp 说。
高效、精简且具有成本效益的工厂维护和机械可靠性必须放在首位。
为了说明他的观点,Keneipp 提供了一个称为“维护冰山”的图表。高于水的是与材料、人工、加班、合同服务以及管理费用和收益相关的直接维护成本。在表面之下,潜在的间接成本与停机时间、设置和启动、错过计划、库存过剩、危机管理、紧急采购以及对生产的整体连锁反应有关。
“间接组件受制于工厂不稳定的设备和流程,”他说。
所有这些浪费都会给系统带来麻烦,并增加运营和维护成本。
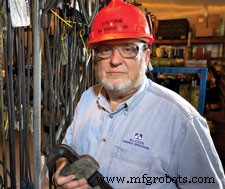
2002 年,这家冶炼厂的总维护成本超过 3500 万美元。每生产一公吨铝的维护成本超过 137 美元的“令人痛苦的高”比率(有关年吨位,请参阅“事实”)使其在全球美铝冶炼厂中排名倒数第二。 2002 年的全球平均价格为每公吨 90 美元。
这家美铝工厂及其领导有两种选择。
“工厂经理 Royce Haws 说我们将降低成本。留在原地不是一种选择。这将会发生,”Keneipp 说。 “我们可以通过聪明的方式或短视的方式来做到这一点。当你近视时,那是可怕的日子。当您只是推迟维护时,很难吸引资金进入工厂来处理需要完成的事情。没有人对这种方法感觉良好。这是人们寻求更好事物的动力。”
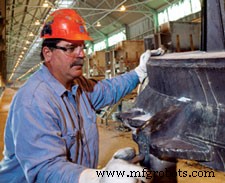
乘风破浪
如果您现在还没猜到,美铝工厂选择了明智的方法来降低维护成本。 2003 年初,维护领导者与生命周期工程 (LCE) 和 Ron Moore Group 的顾问合作,创建了一种称为可靠性卓越流程的方法,该方法在三个“浪潮”中部署。该过程基于这样一种信念,即维护和运营之间必须建立正式、明确的合作伙伴关系。在这种伙伴关系中,运营部门拥有设备并在可靠性方面拥有主要利益。维护是一个平等的合作伙伴,致力于提供及时有效的方法、技能、专业知识和支持。
“这是一个很大的变化,”可靠性工程主管 Joseph Motz 说。 “它曾经是一个相互指责的筒仓环境。”
熔融金属从坩埚中浇注
在铸锭部美铝工厂。
一些例子:
一名操作员注意到一个潜在的问题。没有安排或进行修复。机器坏了。谁的错?
或者,维护出现了两小时的预防性维护工作。在机器中,它发现了其他问题并在 8 小时后完成了 PM 工作,从而影响了产量。谁的错?
在这些情况下,答案是维护和运营。
“我们必须意识到我们都在同一个团队中,”Motz 说。 “我们都是来制造铝的。如果我们走不同的方向,不一起工作,这个过程就行不通。”
三浪方法中的第一浪始于2003年6月。
“第一波是 Ron Moore,”Keneipp 说。 “我们带他来与工厂的主要领导交谈。他挑战了古老的范式。 “你需要更多地采用资产所有者的哲学。” “你在浪费钱。”他摇晃着事情并睁开了眼睛。”
第 2 波于 8 月抵达,并由 LCE 进行了全面的卓越可靠性评估。在两周的时间里,该公司对 90 名运维员工(时薪和薪水)以及工厂控制员进行了长时间的访谈。
该信息导致:
-
财务分析,详细说明与实施成本相比,缩小差距以实现卓越可靠性的估计价值(以投资回报计算形式表示);
- 初步总体规划,概述了弥合差距所需的流程和方法。
“我们想查看我们当前的状况并确定目标状况,”Keneipp 说。 “这两者之间的差距是你的痛苦或收获。是否值得努力弥合差距?我们必须向高级管理层证明这一点。我们必须证明在旧工厂投入资金是有好处的。
“面对所有事实,尽快获得批准才能继续进行。”
第 3 波于 9 月开始。运维负责人:
-
实施总体规划
-
对所有员工进行与提高设备可靠性相关的新角色和职责的教育
-
举办了关于适当的可靠性增强技术的研讨会
-
建立明确的流程和有效的进展措施
“这并不容易。这些东西都不是,”电解车间生产经理 Rodney Cunningham 说。 “但是,如果您有管理承诺以及维护和运营之间的伙伴关系,您成功的机会就会增加。没有这些东西,你就不会成功。”
提高标准
在各个领域建立定义有助于引发改进。一个主要的焦点是定义“什么是可能的?”和“什么是进步?”
一个答案是接受整体设备效率 (OEE) 作为关键的全厂指标。 OEE 跟踪运营损失的来源,包括设备可用性、性能和质量,并以最佳性能的百分比表示。
“它基本上是由过去的一些最佳表现来定义的,”电极生产经理 Tom Svoboda。 “你看到它发生了。这不是虚构的或假设的。无论设备在那个月运行得非常出色,还是您真的掌握了流程,它都发生了。问题是,如果你在那段时间里做了,为什么你不能一直做?”
使用运动类比来说明 100% OEE 的重要性,如果一名跳高运动员通常跳高 6 英尺 6 英寸,但建立了 7 英尺的个人最佳成绩,那么什么特别导致了 100% 的峰值表现。他的训练方式不同吗?他在见面前改变了饮食吗?他穿了不同的鞋子吗?他确实提高了标准。可以学到什么以及可以做些什么来一次又一次地实现这一目标?
维护和运营共同确定工厂功能(例如阳极组装)、流程(矿石卸载)、结果(废料)和单个设备(环炉)的最佳性能。在编制此信息时,确定实现 OEE 目标的结果是每年可以节省 830 万美元的成本。
根据背景信息,定义当前状态并建立目标条件。活动——利用精益制造工具(如改善和持续改进)的工作项目——发生了。对进展进行了衡量和分析。并且,计算了有形的收益。
2004 年,240 万美元的改进与 OEE 收益相关。
更深入地观察并采取行动还降低了冶炼厂的维护费用。在开始可靠性计划后的第一年,费用减少了 190 万美元,从基线数字 3200 万美元减少到 3010 万美元。 2004 年,这个数字又下降了 70 万美元。 2004年每吨生产维护费用的比率也下降到109美元。
“计划”的计划
还作出了重大努力来更好地定义维护要素。具体来说,在这个操作员主导的可靠性系统中,“工作是如何计划的?”以及“工作是如何完成的?”
“回想起来,我们自欺欺人地认为我们很健康,”维护经理丹尼·雷耶斯 (Danny Reyes) 说。 “我们的许多旧指标都脱节了。我们认为我们的“计划和计划工作百分比”为 85%,我们的“PM 完成百分比”为 90%。”
LCE 通知工厂它使用了错误的定义。
“‘计划和计划工作的百分比’实际上只是‘计划的百分比’。计划非常有限,”雷耶斯说。 “这是计划合规性。这些工作中可能有 10% 是计划好的。”
工艺人员(140 人)与规划人员(4 人)的比例为 35:1 是问题的关键。
“它的效果不是很好,”维护规划师 Larry McCubbins 说。 “计划的时间很少。你成了一名调度员,但在这方面并不是很好。”
在这种情况下,反应性环境蓬勃发展。 “我们采用的是‘家庭维护方法’,”Keneipp 说。 “这就是你和我在周六早上处理项目的方式。这真的是无计划且低效的。”
此后,该工厂增加了 3 名计划员,总共 7 名,使 20 比 1 的比例更易于管理。
冶炼维护主管说:“这使这些人能够设置、组织工作、计划、与生产中心安排工作,确保所有零件都在那里,确保设备停机并分配时间。”斯科特·迪恩。
更好规划的其他关键:
-
正式文件现在概述了计划工作的组成部分(请参阅第 14 页的侧栏)。 “我们试图做所有事情的可怜的四个计划者并没有以同样的方式做事,”Deon 说。 “这种新格式现在标准化了如何执行工作。”
-
规划人员现在使用一个正式、安全的区域来进行工作配套。过去,需要的零件和材料是零零碎碎地运送到工作现场。一堆可能会放置数周,直到所有物品都到达。在等待期间,零件或工具被移动、丢失或用于其他工作的情况并不少见。
“计划员在计划工作时,他订购了所有材料并将它们交付到这里,”麦卡宾斯说。 “当工作的所有东西都在这里时,我们将它收集在一两个托盘上。然后手工艺品来把它带到工作现场并进行工作。” -
有效的沟通。
“我曾经认为我知道人们想要什么。这个过程告诉我,我没有,”麦卡宾斯说。 “我不知道他们想要什么,什么适合他们。过去,我计划工作,没有问问题。”
补充道:“与生产分担责任,我们现在知道哪个工作是第一位的。拥有设备的人应该知道什么是最关键的。以前,我不认为我们在猜测。但我们是 100% 吗?可能不会。” -
有重点、有效的每周会议。
“资产所有者主持会议,区域维护规划师/调度员是协调人,”Keneipp 说。 “如果这是一个计划会议,我们会讨论我们将如何做到这一点。如果是安排会议,我们会制定时间表。”
此外,关于如何完成工作,该工厂采取措施记录设备历史记录并标准化维护任务说明。
“在早期,你可以获得记录,但随后文档停止了,”整流站电力工程师 Dan Decastra 说。 “因此,我们在服务器上创建了一个位置并开始记录。对于这个电台,我们创建了一个“坏男孩”列表。我们挑出大问题并从那里开始。现在,您可以回到 2001 年,看看空气开关、触点、变压器和撬块的历史。”
可靠性工程师 Jonathan Fulton 补充道:“如果我们愿意,也许我们三分之一的维护人员可以在明天退休。这对我们来说是一个巨大的潜在责任。而且,很难从外面得到一个优质的工匠。为了解决这个问题,我们正在标准化工作流程并开发设备历史。通过这样做,我们可以让具有技术专长的人尽快跟上进度。”
婴儿床笔记
最后一个改进示例是工厂如何更好地定义谁购买维护产品以及如何花钱购买工具和消耗性材料。
过去,冶炼厂的各种维修人员购买了手动工具、电动工具、安全产品、清洁剂、物料搬运产品和其他一百种必需品。购买的产品存放在设施周围的分散式工具床和许多非官方存放处(储物柜、箱子和小房间)。
“随着工厂不断扩大,面积也不断增加。他们有一个小组,有人负责订购,他们会在这里和那里集中供应,”一般机械师迪克·戴 (Dick Day) 说。 “我们花了大量资金试图为这些卫星婴儿床提供食物。他们没有被管理。人们买了东西,但实际上并不容易获得。”
如果机械师需要特定工具,他会去寻找。它在某处附近。如果他找不到它,他会订购一个。购买的工具可能会在到达他之前消失。这导致了浪费和多余的支出。
为了解决这个问题,建造了一个集中式婴儿床,所有卫星婴儿床和小房间物品都被带到这个安全的门禁区域。
一文不值的进来了。
“我们意识到我们有很多过时的东西 - 一些我们可能在 10 年前就已经拆除的设备,”Keneipp 说。
而且,有价值的东西进来了。
“从木制品中出来的东西真是太神奇了。有人带来了一个柜子,里面有超过 38,000 美元的泵和千斤顶,”成为中央婴儿床的主要服务员的戴说。 “我们开始使用我们拥有的东西。对于某些材料,我们一年内无需订购任何东西。”
今天,Day负责购买这些维修相关的产品。他接收购买的物品,储存物品并根据需要分配它们。
“我们知道我们拥有什么以及它位于何处,”他说。
Day 还为各种产品创建了最小/最大系统,并着手标准化电动工具和焊接用品的品牌。
“对于电动工具,我们主要在 DeWalt 上实现标准化,并且我们正在大量使用他们的无绳工具,”他说。 “对于焊接用品,我们对送丝枪和这些焊枪的更换部件进行了标准化。”
他做好功课并寻找创新方法来削减成本。
几个例子是:
手套 :“我们曾经以每双 12 美元的价格购买一个带有小标签的手套品牌。这就是每个人‘必须拥有的’,”他说。 “你可以以每双 2.67 美元的价格购买带有一点弹性的相同手套。人们喜欢他们。”
液压油 :“我们以每加仑 8 美元的价格购买了它。批量购买,我们现在每加仑可节省 3 美元。我将油倒入可重复使用的水壶中,每罐售价 57 美分。”
乙炔软管 :“我们过去常常购买预先包装在线轴的产品。现在,我们以 500 英尺的卷购买它并切断人们的需求。我们节省了 25%。”
戴说这都是常识。
“我把它看作是我的钱,”他说。 “如果这是我的生意,这就是我的经营方式。”
让他们出汗
通过努力工作、合作伙伴关系、所有权和创新思维,这家美铝冶炼厂变得更加稳定、精益、可预测、可靠和具有成本竞争力。
与 2003 年的基准数据相比,2005 年年初至今的 OEE 成本收益为 440 万美元。
2005 年年初至今的维护费用为年化 2710 万美元,比 2003 年的基准数字减少了 490 万美元。
2005 年第二季度的维护成本为每公吨生产成本 96 美元,并有望在不久的将来达到 87 美元。
LCE 后续评估将该工厂列入“积极条件”类别,目前正在努力提升为“卓越”类别。
有乐观和动力。
“当我 15 年前受雇时,我们说,‘我们是旧技术。我们无法与一些更现代化的设施竞争,”富尔顿说。 “对我来说,奖励是看到我们竞争并提高效率。与 10 或 20 年前建造的工厂相比,我们拥有 40 或 50 年历史的技术生产得更好。”
虽然这家工厂的热量永远不会完全消失,但它正在尽其所能让比赛出汗。
计划作业的特征是什么?
-
对工作有准确的时间估计,以便主管对其何时可以分配任务有合理的期望。
-
在工艺人员、维修/更换零件、工具、支持设备等方面对所需资源有准确的估计。
-
获取所有必要信息(蓝图、许可证、安全相关信息等)。
-
建立完成工作的工作步骤顺序、程序和说明。
-
所有需要的零件和材料都已配备。
-
作为确保计划工作质量的内置检查,定期与主管和/或被指派完成工作的工匠讨论工作的性质。确保对工作范围有充分的了解,并且配套的工作包是完整的。
设备保养维修