通过表面处理和氧化石墨烯夹层实现玻璃纤维-铝层压板的协同分层增韧
摘要
研究了表面处理和夹层对玻璃纤维-铝层压板层间力学性能的协同作用。铝板经过碱性蚀刻处理。同时,在铝板和玻璃纤维增强环氧树脂复合材料之间引入了氧化石墨烯(GO)夹层。采用双悬臂梁和端部缺口弯曲试验来评估玻璃纤维 - 铝层压板的层间断裂韧性。获得的结果表明,夹层的增韧效率取决于铝表面特性以及 GO 负载。进一步的比较表明,在碱蚀刻处理和添加 GO 夹层且 GO 负载量为 0.5 wt% 的试样中获得了最高的 I 型和 II 型断裂韧性,与普通试样相比分别高出 510% 和 381%样品。观察断裂面以进一步揭示加固机制。
介绍
纤维金属层压板(FMLs)是一种新型的混合轻质复合材料,由金属基材和纤维增强塑料(FRPs)组成[1]。由于混合结构,FML 提供了优异的机械性能,包括高比强度和刚度、良好的抗疲劳性和出色的损伤容限 [2, 3]。然而,由于金属片和复合层之间的物理性能差异,FML 的弱界面结合可能导致分层和脱粘失败[4]。因此,提高FMLs的层间力学性能势在必行。
为了提高FMLs的层间力学性能,一系列的表面处理方法,如酸或碱蚀刻[5,6,7]、阳极氧化[8]、激光烧蚀[9、10]、硅烷偶联剂处理[11, 12] 和大气压等离子体 [13] 已被提议用于改变金属板的表面形态。在这些方法中,碱蚀刻被认为是一种简单有效的方法,它可以去除金属表面较弱的天然氧化层,同时形成粗糙的表面和稳定的氧化层,以加强界面结合。如今,纳米技术的发展极大地扩展了纳米材料在航空航天[14]、电子器件[15]、能源[16]和环境[17]等各个领域的应用领域。将纳米材料掺入层间层是通过改性富树脂区来改善层压复合材料层间性能的另一种有效方法。常见的交错纳米材料,如纳米粘土[18]、气相生长碳纤维[19]和碳纳米管[20],已广泛应用于FML。
石墨烯由单层碳原子组成,表现出超高的机械 [21]、电学 [22] 和热学 [23] 特性,这使其成为改性聚合物基质的有希望的候选者。拉菲等人。 [24]通过溶液共混制备了用石墨烯增强的环氧树脂基块状复合材料。结果表明,纳米复合材料的拉伸强度和断裂韧性分别增加了 40% 和 53%。 Kostagiannakopoulou 等。 [25]采用石墨烯作为基体中的增韧剂来制备碳纤维增强聚合物,并观察到层间断裂韧性增加了 50%。然而,石墨烯的增韧效率取决于石墨烯在聚合物基体中的分散状态。石墨烯的表面化学性质会影响其与聚合物基体的界面相容性,进而导致石墨烯的分散性较差 [26]。作为石墨烯的衍生物,氧化石墨烯(GO)表面含有多种含氧基团(羟基、环氧化物、羰基和羧基),与石墨烯相比,在聚合物基体中具有更好的分散性和相容性。由于其潜在优势,GO 已成为聚合物复合材料中的有效增强材料 [27,28,29]。据报道,用氧化石墨烯夹层改性的碳纤维层压板显着增加了 170.8% 的模式 I 层间断裂韧性 [30]。帕塔克等人。据报道,通过加入 0.3 wt% GO,碳纤维复合材料的弯曲模量、弯曲强度和层间剪切强度得到了全面改善 [31]。然而,据我们所知,迄今为止尚未研究过由 GO 夹层增韧的 FML 的层间机械性能。此外,金属板表面处理与GO插页的协同效应尚未得到很好的理解。
本文研究的 FML 以玻璃纤维-铝层压板(GFRP/Al 层压板)为基础,该层压板已广泛应用于航空航天和汽车工业等各个领域。通过结合碱蚀刻处理和 GO 增强环氧树脂夹层,系统地研究了 GFRP/Al 层压板的 I 型和 II 型层间断裂韧性。此外,还进行了各种表征以揭示协同增韧机制。
方法/实验
材料
天然石墨薄片(XF051,100 目)购自南京新飞纳米材料科技有限公司,用于通过改良 Hummers 法制备氧化石墨烯 [32]。本研究中使用的环氧粘合剂是双酚 F 的二缩水甘油醚。 EPON862。选择聚酰胺(Epikure3140A)作为固化剂。选择厚度为 2.5 mm 的铝合金(7075)板作为 FML 的金属部分。单向玻璃纤维预浸料(GFRP 预浸料)由中国威海光威复合材料有限公司提供。所有其他材料,例如氢氧化钠 (NaOH)、N ,N -二甲基甲酰胺(DMF)、丙酮、盐酸(37 wt%)和三氧化铬,由成都科隆化学试剂有限公司(中国)提供。
标本准备
GFRP/Al 层压板的制造示意图如图 1 所示。首先,铝板的表面处理按以下步骤进行: (a) 铝板用丙酮冲洗脱脂,然后在烘箱中干燥为了去除水分,(b) 将铝板浸入 0.1 M NaOH 溶液中,并在室温下超声处理 30 分钟以改变铝板的表面形态,(c) 取出处理过的铝板并在蒸馏水中超声处理水直至铝与 NaOH 的反应终止,并且 (d) 将洗过的铝板在 60 °C 下干燥 1 小时。关于碱蚀刻表面处理的更多细节可以在参考文献中找到。 [5].
<图片>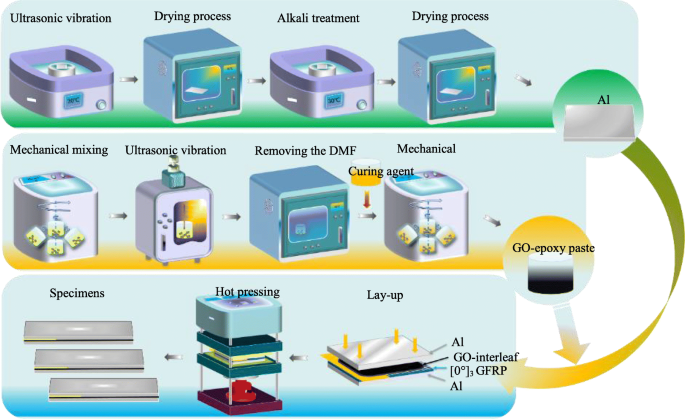
试件制作及热压工艺示意图
图>然后,制备 GO 增强环氧树脂糊作为增韧夹层。 GO interleaf 的详细准备过程与我们之前的工作类似[30]。主要步骤包括(a)通过机械混合和超声振动制备GO/DMF悬浮液,(b)将环氧树脂倒入GO/DMF悬浮液中并通过行星串和超声混合,(c)加热上述混合物以去除DMF,(d)在不断搅拌下加入固化剂。
最后,使用热压方法制备 FML,如图 1 所示。主要步骤包括: (a) 三堆单向 GFRP 预浸料通过叠层工艺堆叠在两块铝板之间。在制造过程中,使用钝刀片在铝板和GFRP预浸料的界面上小心涂抹得到的GO-环氧树脂糊,其中环氧树脂的面积密度设置为恒定值约167 g/m 2 . (b) 插入离型膜以形成初始裂纹。 (c) FMLs由聚酰亚胺薄膜包裹并在130 °C的温度和0.12 MPa的压力下固化。
为了探讨表面处理和 GO-环氧树脂夹层对 FMLs 断裂韧性的影响,制备了五种类型的试样,即普通、GO0.5%、SH-GO0%、SH-GO0.5%、和SH-GO1%,其中“SH”表示Al板的碱蚀处理,“GO”表示GO-环氧树脂夹层,“GO”后面的百分比表示GO在环氧树脂中的重量分数。
实验测试和表征
根据日本工业标准 (JIS) K7086 [33],进行双悬臂梁 (DCB) 和端部缺口弯曲 (ENF) 测试以测量 GFRP/Al 层压板的 I 型和 II 型层间断裂韧性。 DCB 和 ENF 试样的配置如图 2 所示。详细的测试程序和断裂韧性计算方法与参考文献中的相似。 [33].
<图片>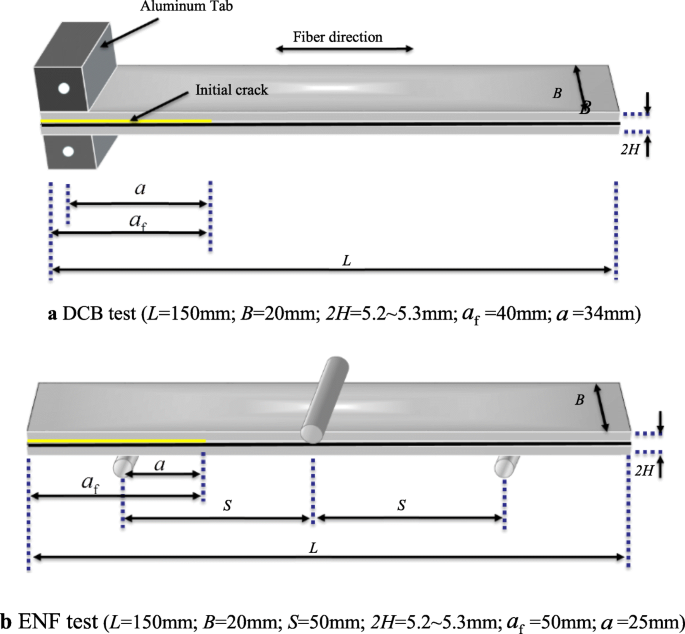
a 的样品示意图 DCB 和 b 易恩孚测试
图>通过扫描电子显微镜(SEM)表征石墨薄片、GO、铝片和测试样品的断裂表面的表面形貌。同时,通过透射电子显微镜(TEM)和原子力显微镜(AFM)观察GO片的纳米结构。 GO 和铝基板的化学结构在 ESCALAB 250Xi XPS 系统(Thermo Electron Corporation,USA)上进行表征。此外,还分别利用光学干涉轮廓仪和接触角测角仪研究了铝板的表面粗糙度和润湿性能。
结果与讨论
GO 的特征
石墨和 GO 薄片的表面形貌通过 SEM 和 TEM 表征,如图 3 所示。可以在图 3a 中观察到石墨薄片的多层结构,而图 3a 中 GO 的 SEM 和 TEM 图像可以观察到。图3b和c表现出薄层结构。这表明石墨的多层结构是分层的,并且已成功合成氧化石墨烯。图 3d 显示了 GO 纳米片的 AFM 图像。制备的GO的厚度约为0.968 nm,表明从石墨完全剥离后获得了单层氧化石墨烯纳米结构。此外,GO的分散状态在聚合物的增韧中起着至关重要的作用。 GO 的分散性差可能会对应力从树脂到 GO 纳米片的转变产生不利影响。因此,需要对分散的 GO 进行表征和评估。图 3e 和 f 显示了分散在环氧树脂中后的 GO 片材的微观结构。 GO以0.5 wt%的浓度掺入在树脂中表现出良好的分散性,而在较高浓度(1.0 wt%)下可以观察到GO的轻微聚集,这可能导致应力集中,从而削弱树脂的强度和韧性环氧树脂。
<图片>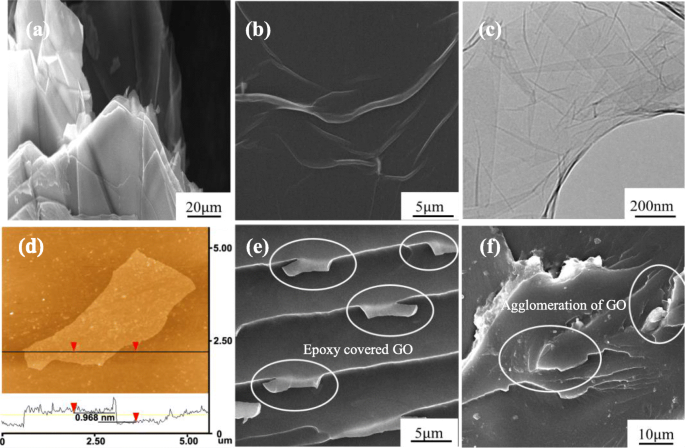
a 的 SEM 图像 石墨薄片。 b 去表。 c GO 的 TEM 图像。 d GO 的 AFM 图像。 e 环氧树脂中的 GO 片材(0.5 wt%)。 f 环氧树脂中的GO片材(1.0 wt%)
图>GO 表面的化学结构是影响聚合物中 GO 增韧效率的另一个重要因素,它是 GO 与树脂基体之间界面相互作用的原因 [30, 31, 34]。 X射线光电子能谱(XPS)用于鉴定所制备的GO的表面化学性质。如图 4 所示,GO 的 C 1s 光谱被分成四个峰,分别归属于四种类型的碳键:(1) C-C/C=C (284.5 eV),(2) C-O ( 286.9 eV),(3)C=O(288.2 eV),和(4)O-C=O(289 eV)[35]。氧化官能团的存在有利于GO的分散和GO与聚合物基体之间的结合强度[30,31,34]
<图片>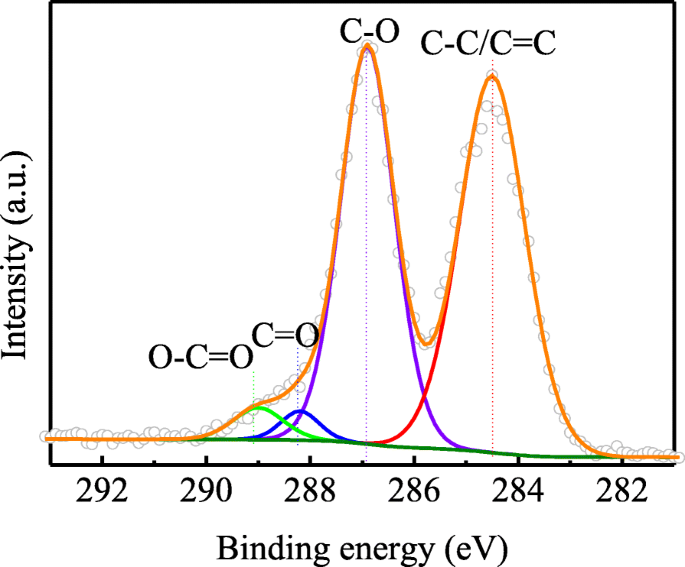
GO片的XPS C1s光谱
图>铝合金表面的理化性质
通常,FRP 复合材料与金属之间的界面脱粘包括界面和内聚破坏,这通常受金属板表面特性的影响。因此,通过各种测量仪器对铝合金表面的表面显微组织、粗糙度、化学成分和润湿性等理化性能进行了表征。
图 5 为碱蚀前后铝合金板的表面形貌和显微组织。可以看出,经过碱蚀处理的铝合金表面比脱脂后的铝合金表面更粗糙。碱蚀处理后的铝合金表面可以观察到许多微尺度孔穴,有利于环氧树脂和GO的填充,形成机械互锁,增强复合材料/金属界面的结合强度。 7, 19, 36]。此外,还使用光学干涉轮廓仪测量了碱蚀刻前后铝合金板的表面轮廓。相应的表面粗糙度值(R 一 , R q , 和 R z ) 总结在表 1 中,其中 R 一 表示轮廓的算术平均偏差,R q 是均方根粗糙度和 R z 表示不规则的十点高度。从表 1 可以看出碱蚀前后的测量值存在显着差异,这与图 5 中的 SEM 观察结果一致。碱蚀表面的高粗糙度意味着比表面积的增加,这是有益的用于铝合金薄板与聚合物基体之间的机械联锁。
<图片>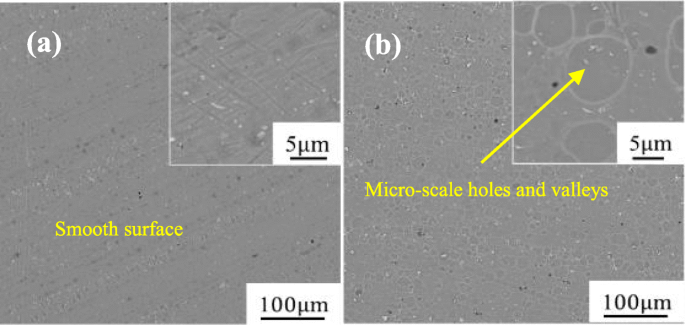
a后Al表面的SEM图像 脱脂和b 碱蚀
图> 图>进行XPS分析不同表面处理的铝合金表面的化学改性。图 6 显示了未蚀刻和蚀刻铝合金表面的 Al 2p 和 O 1s 的窄扫描光谱。图 6a 显示了未蚀刻表面的去卷积 Al 2p 电离光谱,其中只有一个峰的结合能为 74.4 eV,对应于 γ-氧化铝 (γ-Al2O3) [37]。未蚀刻表面的 O 1s 光谱分为 2 个峰,分别归属于 Al2O3 (531.3 eV) 和氢氧化铝 (533.1 eV) [13]。
<图片>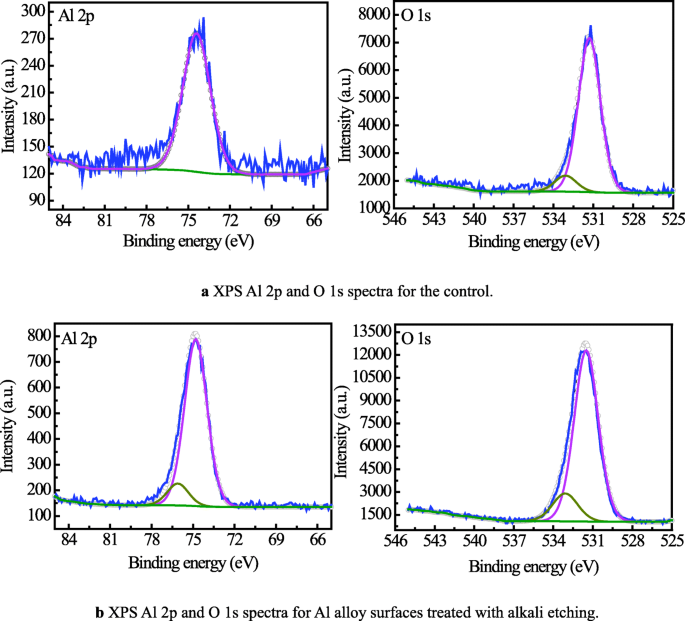
铝合金表面XPS光谱窄扫描
图>图 6b 显示了蚀刻表面的去卷积 Al 2p 电离光谱,其中位于 74.8 eV 的第一个峰与 Al2O3 相关,而位于 76.1 eV 的峰对应于氢氧化铝 [38]。蚀刻表面的 O 1s 光谱显示出两个峰,一个是 Al2O3 (531.5 eV),另一个是氢氧化铝 (533.1 eV) [13]。比较未蚀刻和蚀刻的铝合金表面的结果,Al 2p 结合能的变化意味着铝合金的表面化学性质已因表面处理而改变 [6]。同时,蚀刻表面的O 1s峰的氢氧化物与氧化物强度比高于未蚀刻表面,由于氢氧化铝和环氧树脂上的羟基之间形成更多的氢键,因此可以提高界面粘合力分子[13]。
为了研究表面处理对铝合金表面润湿性的影响,将标准液滴滴在测试样品的表面上以测量接触角。图 7 显示了碱蚀刻前后铝合金表面的静态接触角图像。可以发现,碱处理后的铝板表面接触角更小,说明碱蚀处理后的铝合金表面润湿性更好。润湿性的增加也可能有助于提高界面结合强度[6]。
<图片>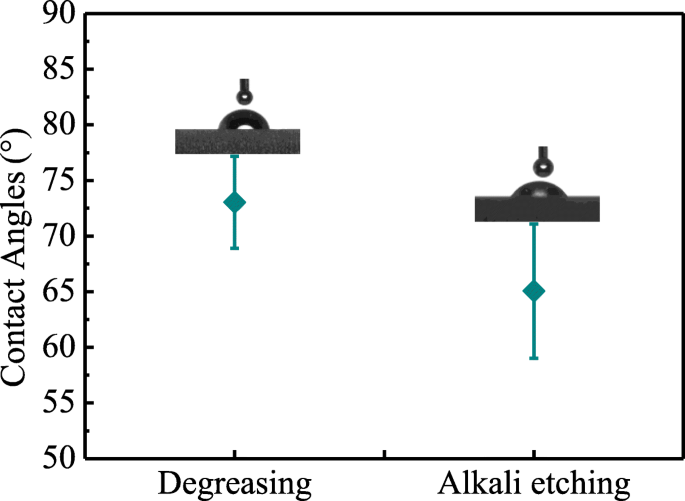
不同表面处理的铝合金表面水滴接触角
图>Mode-I 层间断裂韧性
DCB 测试是在不同类型的 GFRP/Al 层压板上进行的。图8 负载P的关系 和裂纹张开位移(COD)。可以求出载荷和裂纹张开位移的总体趋势(P -COD) FMLs 试样的响应几乎相似,即施加的载荷首先线性增加,然后以非线性模式略微增加,直到载荷达到最大值,然后在最后阶段逐渐下降。由于裂纹扩展起始的不确定性,临界载荷 (P C) 定义为 P 的交集 -COD 曲线对应的顺应性比初始曲线高 5% [33]。
<图片>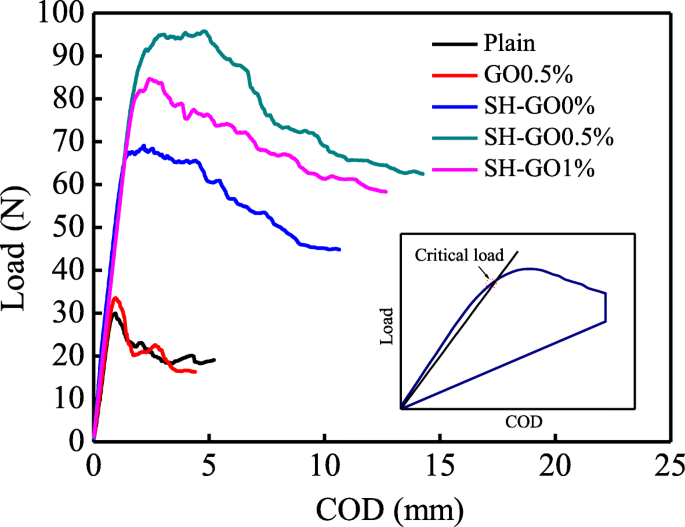
代表性载荷和裂纹张开位移 (P -COD) DCB 试验中不同试样的曲线
图>图 9 表示临界负载 P C 的测试样本。我们可以看到 P GO0.5%试件的C与平原相似,远低于其他类型试件。铝合金经碱蚀预处理后,P SH-GO0% 试样的 C 显着增加,表明表面处理在界面粘附中发挥了重要作用。值得注意的是临界载荷P SH-GO0.5% 试样的 C 在碱蚀刻和添加 0.5 wt% GO 相结合时进一步增加,获得最高的 P C 比普通和 GO0.5% 试样高约 160%,这表明表面处理和 GO 夹层之间可能存在协同增韧作用。然而,P C随着GO含量的进一步增加(SH-GO1%)而下降,这可能是由于GO在较高浓度下的团聚所致。
<图片>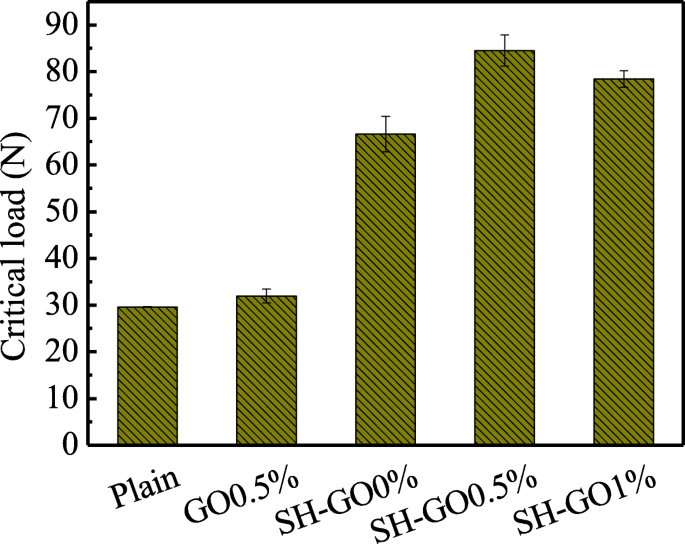
临界负载P DCB试验中各种试样的C
图>图 10 表示作为裂纹扩展增量 ∆a 的函数的 I 型断裂韧性 (R -曲线)用于测试样品。可以看出,对于普通试样和 GO0.5% 试样,I 型断裂韧性与裂纹扩展增量 Δa 无关 ,这也表明脱脂铝合金和玻璃纤维层压板之间的界面结合较弱。然而,对于其他类型的试样,可以观察到典型的断裂行为,其中I型断裂韧性首先随着裂纹扩展而增加,然后由于玻璃纤维桥接效应而变得稳定。
<图片>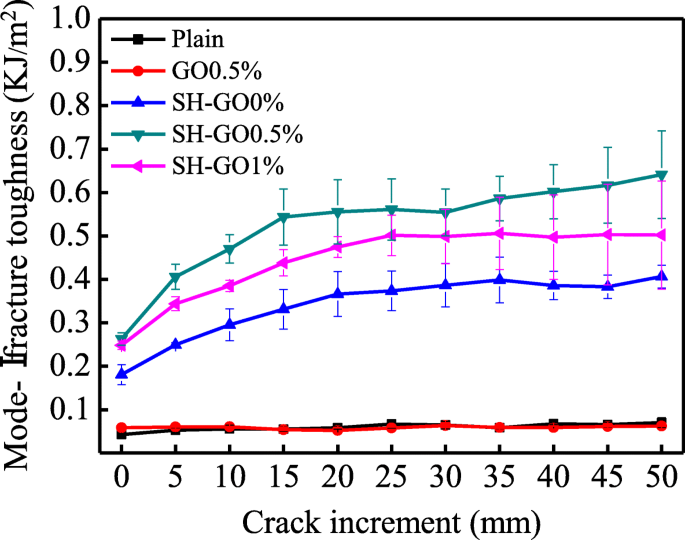
R 的比较 -DCB试验中各种试样的曲线
图>为了更好地了解表面处理和 GO 夹层对 GFRP/Al 层压板的层间力学性能的影响,I 型断裂韧性 G IC和抗断裂性G IR 总结在图 11 中,其中 G IC 是 R 上的起始值 -曲线和G IR为裂纹扩展范围Δa内五点的平均值 从 20 到 40 mm。从图11可以看出,G没有显着差异 IC 和 G 普通试样和 GO0.5% 试样之间的 IR。然而,G 大幅增加了 225% 和 600% IC 和 G 当用碱性化学蚀刻处理铝合金板时,可以观察到 SH-GO0% 试样的 IR。这种增强是由于通过“I 型层间断裂韧性”部分所述的碱性蚀刻处理改善了铝合金板的表面形貌和化学性质以及润湿性。对于协同增韧试样(SH-GO0.5% 和 SH-GO1%),G IC 和 G IR 远高于仅用表面处理增韧(SH-GO0%)或仅用 GO 夹层(GO0.5%)增韧的试样,这可能归因于表面处理(增强的界面粘附)和GO interleaf(增韧环氧树脂基质)。最大G IC 和 G 在 SH-GO0.5% 试样中观察到的 IR 为 263 J/m 2 和 590 J/m 2 ,分别比平原高约510%和820%。
<图片>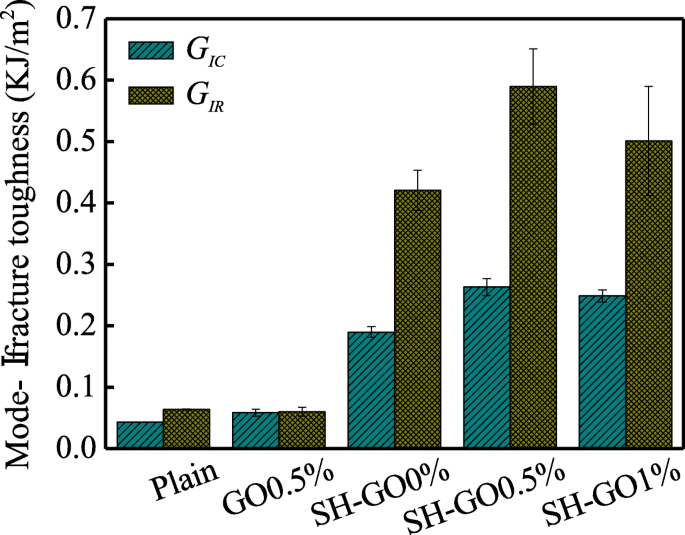
不同试样的I型断裂韧性和抗力比较
图>Mode-II 层间断裂韧性
ENF 试件的 Mode-II 载荷-挠度曲线如图 12 所示。通常情况下,载荷-挠度曲线在初始阶段呈现线性响应,然后是非线性响应,直到最大载荷,然后突然下降最后阶段。图 13 显示了临界负载 P C和II型层间断裂韧性G 根据载荷-挠度曲线计算出的测试样品的 IIC。需要注意的是,定义临界载荷的准则P ENF 试样的 C 类似于 DCB 试样的 C。我们可以看到 G IIC和P ENF 试样的 C 与 DCB 试样的 C 具有相同的趋势。 SH-GO0.5%试样的II型断裂韧性和临界载荷的最大值分别比普通试样高381%和99%。
<图片>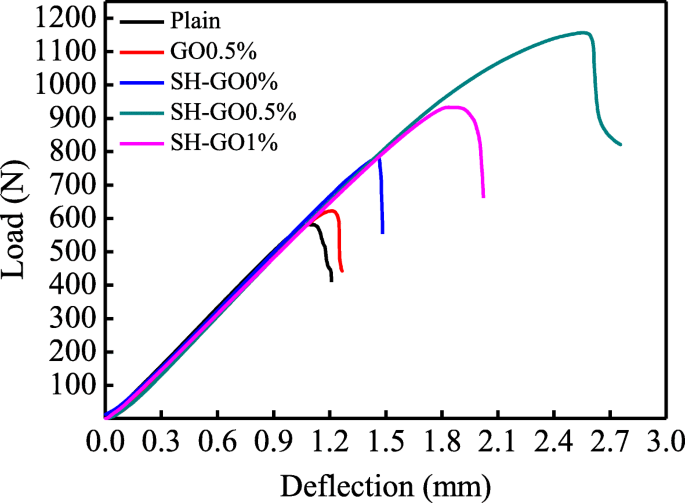
易恩孚试验中不同试样的代表性载荷-挠度曲线
图> <图片>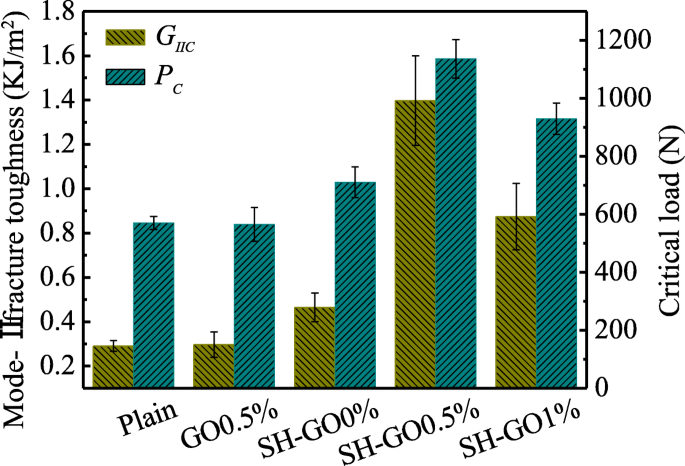
Ⅱ型断裂韧度比较G IIC和临界负载P ENF试验中各种试样的C
图>裂缝形态观察
为了进一步揭示增韧机制,通过扫描电镜观察了测试GFRP/Al层压板的断裂形貌。
图 14 显示了 DCB 测试后 GO0.5%、SH-GO0%、SH-GO0.5% 和 SH-GO1% 试样的断裂表面。对于 GO0.5% 试样(见图 14a 和 b),断口表面光滑,没有任何可见的玻璃纤维或环氧树脂附着在铝合金板表面。 GO0.5% 试样的破坏类型是粘合破坏。对于 SH-GO0% 试样(见图 14c 和 d),可以观察到一些断裂的纤维和环氧树脂附着在表面或嵌入微孔中,这表明碱蚀刻可以促进铝之间的机械互锁合金板和聚合物基体,进而改善它们之间的界面结合。 SH-GO0% 试样的破坏类型是内聚性和粘合剂的组合。与界面破坏相比,由树脂分子脱键引起的内聚破坏可能消耗更多的能量 [19],表明 SH-GO0% 试样与 GO.5% 试样相比具有更高的 I 型断裂韧性。对于 SH-GO0.5% 和 SH-GO1% 试样(见图 14e-h),可以观察到更不规则和更粗糙的断裂形态,这将产生更大的断裂面积,并且需要更高的驱动力和能量。 SH-GO0.5%和SH-GO1%试样的破坏类型几乎为内聚破坏,表明GO夹层的加入可以进一步提高经过表面处理的GFRP/Al层压板的层间断裂韧性。可能的原因如下:由于其优异的机械性能,GO可以通过诱导裂纹偏转和裂纹桥接效应来有效提高环氧树脂的韧性[30],这通常需要更高的驱动力和更高的断裂能。同时,GO片表面的官能团将有助于GO与环氧树脂之间的强界面结合,这可能在将GO从环氧树脂基质中拉出的过程中消耗更多的能量。此外,GO 的添加增加了树脂基质的反应性官能团 [39, 40]。因此,与SH-GO0%试样相比,SH-GO0.5%和SH-GO1%试样的I型断裂韧性进一步提高。
<图片>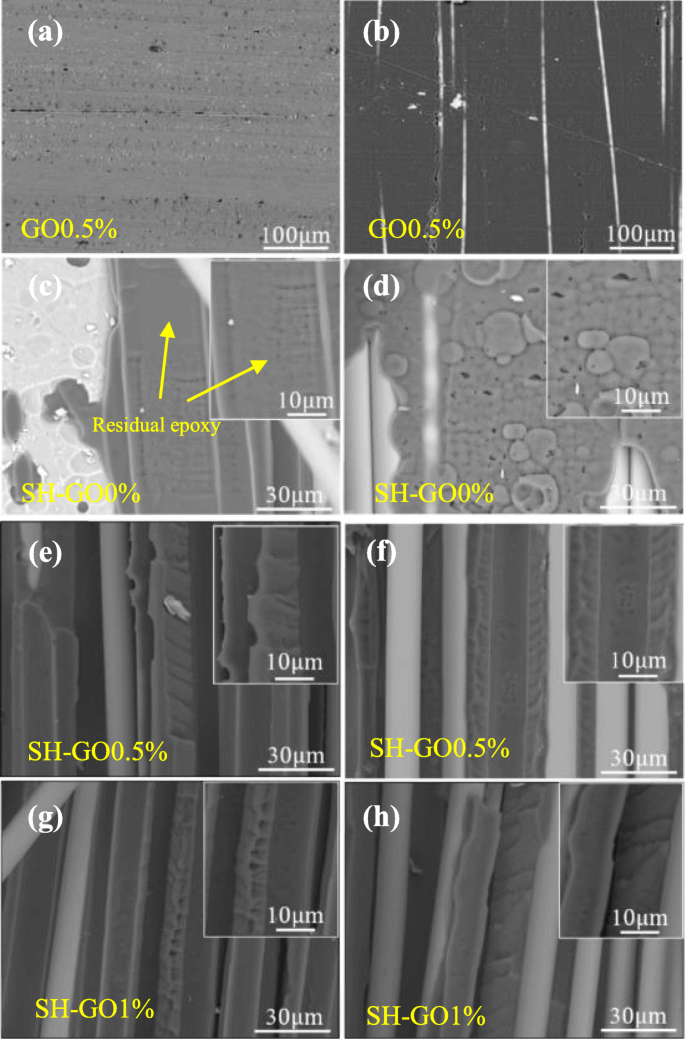
I 型 GFRP/Al 层压板的断裂面。 a, b GO0.5%。 c , d SH-GO0%。 e , f SH-GO0.5%。 g , h SH-GO1%(左,Al侧;右,复合侧)
图>基于上述分析,已经证明了表面处理和 GO-环氧树脂夹层对提高 Al/GFRP 层压板的 I 型层间断裂韧性的协同作用。然而,过量的 GO 可能会对断裂韧性产生负面影响。由于GO的聚集可能导致应力集中并降低环氧树脂的韧性(见图3),因此SH-GO1%试样的I型断裂韧性低于SH-GO0.5%试样。>
SEM还用于研究测试样品的ENF断裂表面。对于 GO0.5% 试样(图 15a 和 b),Al 板和 GFRP 侧的断裂表面相对光滑,这与 GO0.5% 试样的 DCB 断裂形态相似。对于 SH-GO0%(图 15c)、SH-GO0.5%(图 15e)和 SH-GO1% 试样(图 15g),可以观察到粘附在铝板表面上的断裂纤维和残留环氧树脂),这意味着与 GO0.5% 试样相比,发生内聚破坏和更高的断裂韧性。此外,SH-GO0.5% 和 SH-GO1% 试样在铝板和复合材料侧面有很多典型的剪切唇,表明损伤区增加,塑性变形较大,这可能导致具有比 SH-GO0% 更高的 II 型断裂韧性。此外,GO的聚集也可能是SH-GO1%试样与SH-GO0.5%试样相比II型断裂韧性较低的主要原因。
<图片>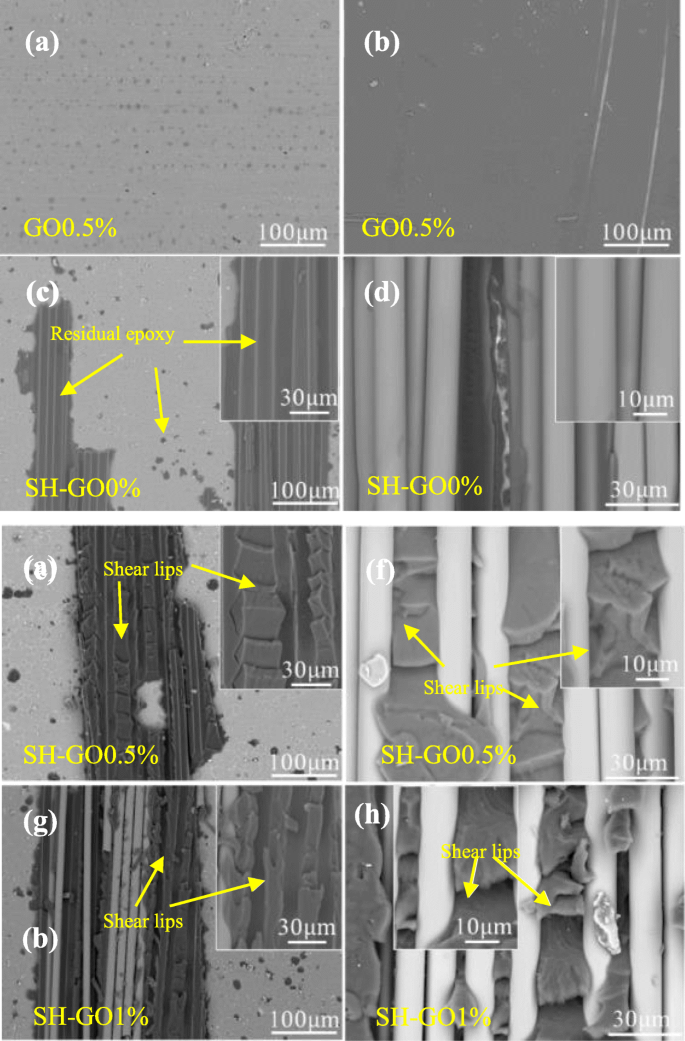
模式 II GFRP/Al 层压板的断裂面。 一 , b GO0.5%。 c , d SH-GO0%。 e , f SH-GO0.5%。 g , h SH-GO1%(左,Al侧;右,复合侧)
图>结论
在这项研究中,表面处理,例如碱蚀刻和 GO-环氧树脂夹层相结合,协同提高了 Al/GFRP 层压板的层间机械性能。 DCB和ENF结果表明,经过碱蚀处理和GO0.5%-epoxy interleaf的试样具有最高的I型和II型层间断裂韧性,分别比普通试样高510%和381%。标本,分别。此外,采用不同的表征技术研究了铝板的表面性能和测试层压板的断裂表面,以揭示协同增韧机制。
数据和材料的可用性
本文包含支持本文结论的数据集。
缩写
- Al:
-
铝
- FRPs:
-
Fiber-reinforced plastics
- GFRP/Al laminates:
-
Glass fiber-aluminum laminates
- GFRP prepregs:
-
Glass fiber prepregs
- 开始:
-
氧化石墨烯
- DCB:
-
Double cantilever beam test
- ENF:
-
End-notched flexure test
- XPS:
-
X射线光电子能谱
- SEM:
-
扫描电子显微镜
- TEM:
-
透射电子显微镜
- 原子力显微镜:
-
原子力显微镜
- FMLs:
-
Fiber metal laminates
- NaOH:
-
Sodium hydroxide
- DMF:
-
N ,N -dimethylformamide
- JIS:
-
Japanese Industrial Standards
- P -COD:
-
Load and crack opening displacement
- G IC :
-
Mode-I fracture toughness
- G IR :
-
Mode-I fracture resistance
- G IIC :
-
Mode-II fracture toughness
- P C :
-
Critical load
- γ-Al2O3:
-
γ-Aluminum oxides
- SH:
-
Alkali etching treatment of Al plates
- R 一 :
-
The arithmetic average deviation of the profile
- R q :
-
The root mean square roughness
- R z :
-
The ten-point height of irregularities
纳米材料
- 扬声器和耳机中的石墨烯
- 钛酸盐纳米管装饰氧化石墨烯纳米复合材料:制备、阻燃和光降解
- 通过镀金和等离子处理调整聚醚醚酮的表面化学
- 石墨烯和氧化石墨烯的体外和体内生物安全和抗菌能力
- 石墨烯/WO3 和石墨烯/CeO x 结构作为超级电容器应用电极的评估
- 纳米级 CL-20/氧化石墨烯的一步球磨制备显着降低粒径和灵敏度
- 通过球形和夹心结构石墨烯/Sio2 支撑制备超高分子量聚乙烯/石墨烯纳米复合材料的原位聚合
- 通过海藻酸钠电解质-磺化氧化石墨烯生物膜增强质子电导率和降低甲醇渗透率
- 氧化石墨烯的低温还原:电导率和扫描开尔文探针力显微镜
- 石墨烯上金属纳米粒子中的电磁场再分布
- 由膜表面上石墨烯片的布朗运动和非布朗运动引起的纳米水泵
- 共价改性氧化石墨烯和混合基质薄膜复合膜中的本征微孔聚合物 (PIM-1)